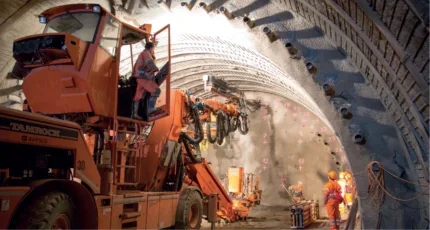
Fire safety is transforming. As tunnels grow larger and more complex, and as equipment becomes more sophisticated, the industry faces new fire risks that demand a shift in how suppression systems are designed and implemented.
The expectations for fire suppression have never been higher in terms of performance, environmental sustainability, compliance with the strictest certifications, and the ability to integrate seamlessly into modern tunnel operations.
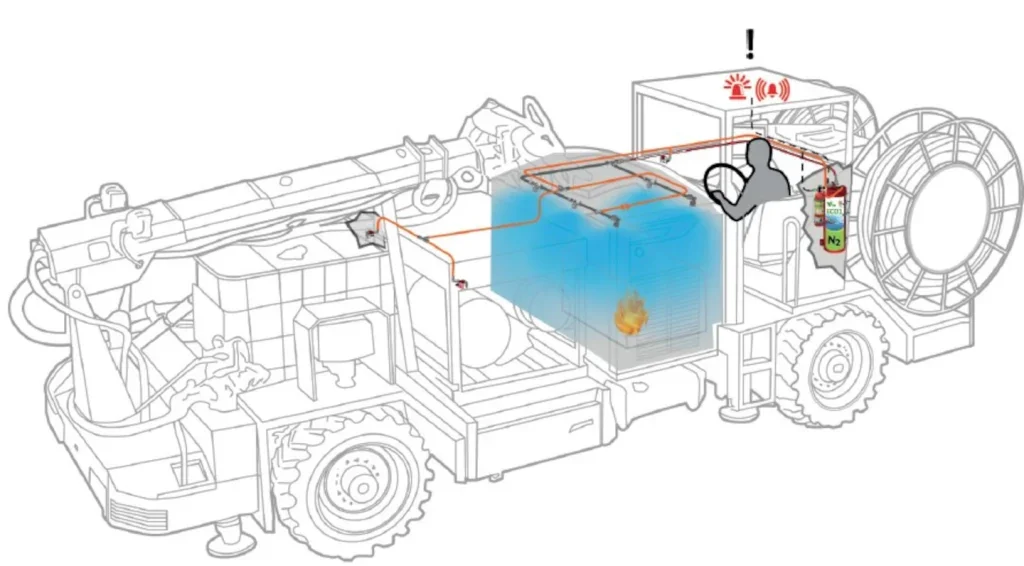
The industry has relied on conventional suppression methods, typically dry chemical or foam-based systems for years. While these approaches have been adequate to some extent, they come with significant challenges:
- extensive clean-up
- high maintenance demands
- limited effectiveness in mitigating re-ignition risks.
Water mist, long recognised for its unique cooling and oxygen-displacing properties, is now emerging as the next-generation solution. And yet, not all water mist systems are created equal. Certification and rigorous real-world testing remain the only objective benchmarks of system reliability.
CERTIFICATION: THE TRUE BENCHMARK
Fire suppression in heavy-duty environments requires validation beyond marketing claims. The difference between a tested and certified system and one that merely claims performance, on paper, can mean either protection or failure.
Pursuing tests and certification, Fogmaker International has achieved distinction of approvals for high-pressure water mist system under FM 5970, SPCR 199, UL, and AS5062, along with SPCR 197. This gives a positioning with the most comprehensively certified water-based suppression system.
For tunnel operators, the different certifications mean:
- FM 5970 – meets the highest international benchmarks for fire suppression in heavy-duty mobile equipment.
- SPCR 199 and UL – validate performance under extreme conditions (e.g., vibration, shock, corrosion).
- SPCR 197 – independently approved non-electric detection mechanism, which adds a critical layer of reliability.
- AS5062 – aligns with stringent Australian mining and tunnel equipment standards.
Each certification represents extensive testing to ensure the system performs effectively in real-world conditions. Therefore, the certifications are not check boxes but result from rigorous validation in environments that simulate actual fire scenarios.
TRENDS IN FIRE SUPPRESSION FOR TUNNELLING
The evolution of fire suppression technology in tunnelling is about more than compliance; it is about meeting the growing complexity of tunnel construction and operations.
1. Fixed and Mobile Suppression Systems
Tunnels present unique fire risks, from vehicle fires to overheating electrical systems. Unlike mining, where mobile equipment fire suppression is the primary concern, tunnelling requires fixed suppression systems for tunnel infrastructure and also mobile systems for equipment during the construction phase, such as tunnel boring machines (TBMs), drill rigs, locomotives, and transformers.
We see a growing trend of integrating fire suppression into tunnel projects from the early construction phase, ensuring protection for mobile equipment during excavation and fixed infrastructure for the long-term operational lives of the underground assets.
2. High-Performance in Harsh Environments
Tunnel environments are extreme, with high temperatures, confined spaces, and continuous vibrations. This requires suppression systems that:
- Function under high pressure to ensure mist penetration in complex areas.
- They are resistant to shock, vibration, and corrosion.
- They are compact and lightweight, without adding excessive weight to vehicles.
Technology has been developed to enable water mist systems to function at high pressure, ensuring complete and adequate fire suppression, even in the most challenging tunnel conditions.
3. Toward Sustainable Suppression Agents
Environmental considerations are driving a shift away from chemical-based suppression agents. Foam-based systems have been widely used, but many have been linked to long-term ecological contamination.
Fogmaker’s Eco 1 water-based suppression fluid is 100% PFAS-free and certified by GreenScreen (see box). With increasing restrictions on chemical-based suppression agents, tunnel operators must adopt futureproof solutions that align with global sustainability regulations.
4. Fire Prevention as a Non-Negotiable Requirement
Regulations around fire suppression in tunnel operations are becoming stricter, making suppression systems mandatory rather than optional safety measures. Demand and solutions include:
- Many tunnel authorities are now mandating fire suppression systems in underground mobile equipment.
- Original Equipment Manufacturers (OEMs) are integrating fire suppression as a standard feature in new machines.
- The adoption of intelligent monitoring systems for real-time detection and remote diagnostics is increasing.
As fire risk mitigation becomes a regulatory standard, operators must move beyond outdated suppression technologies and embrace modern, high-performance solutions.
SETTING A NEW STANDARD
The fire suppressions system described can simultaneously attack all three elements of the fire triangle: heat, oxygen, and fuel. They do so while offering the following features:
- Rapid Cooling and Re-Ignition Prevention – Unlike foam or powder-based alternatives, the fine cloud of water mist absorbs massive amounts of heat in seconds, reducing temperatures to prevent re-ignition, which is essential in confined tunnel environments.
- Environmentally Sustainable – Traditional suppression systems often leave corrosive residues or require extensive clean-up, leading to costly downtime. The PFAS-free ECO1 water-based fluid, certified by GreenScreen, is non-toxic, leaves no destructive residues, and aligns with global sustainability initiatives.
- Compact, Scalable, and Versatile – The system’s compact design allows it to be installed in various applications, from TBMs and small locomotives used in tunnel works to transformers and ventilation shafts, which ensures that protection is not limited to vehicles alone.
A NEW CHOICE FOR TUNNEL OPERATORS
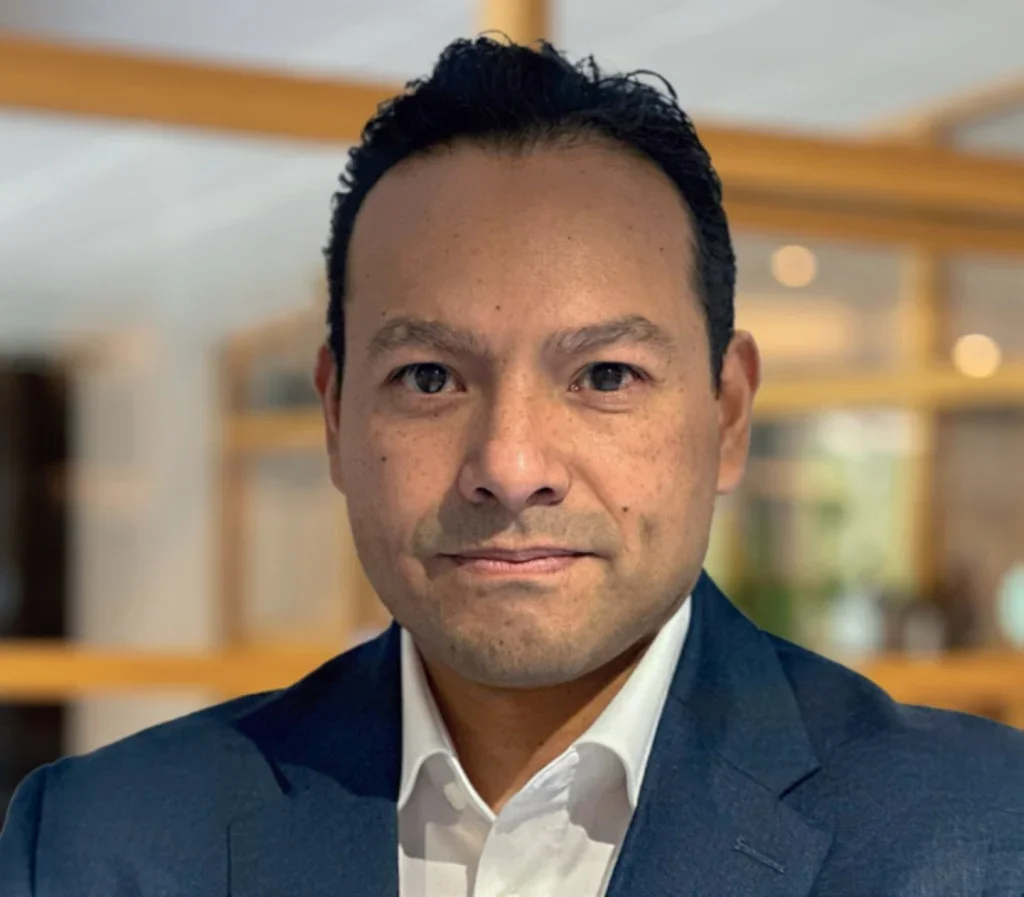
For decades, tunnel operators have had only two main suppression options: powder-based systems or foambased systems. The introduction of high-pressure water mist now provides a third option that combines rapidfire suppression, cooling, and oxygen displacement in a way that traditional systems cannot match.
The question is no longer whether fire suppression is necessary. Regulations and safety demands have already determined those necessities. The real question, therefore, when seeking the best protection for people and assets while ensuring operational efficiency is: which system?
Tunnel operators can choose from:
- Powder-based fire suppression, which creates extensive contamination, leading to high maintenance costs.
- Foam-based fire suppression, which offers limited cooling and is sometimes environmentally concerning.
- High Pressure Water Mist, which cools, displaces oxygen, and suppresses fuel—all in a single solution.
The high pressure, water mist fire suppression system has been rigorously tested and validated.
FOGMAKER GAINS FM APPROVAL FOR FIRESUPPRESSION SYSTEM
Last September Fogmaker International announced it had received FM approval for its high pressure heavy duty mobile equipment (HDME) fire-suppression system.
The testing and approval were performed with the company’s new Eco 1 suppressant – a water-based liquid for use under high pressure that is 100% PFAS-Free and GreenScreen certified at the Silver level.
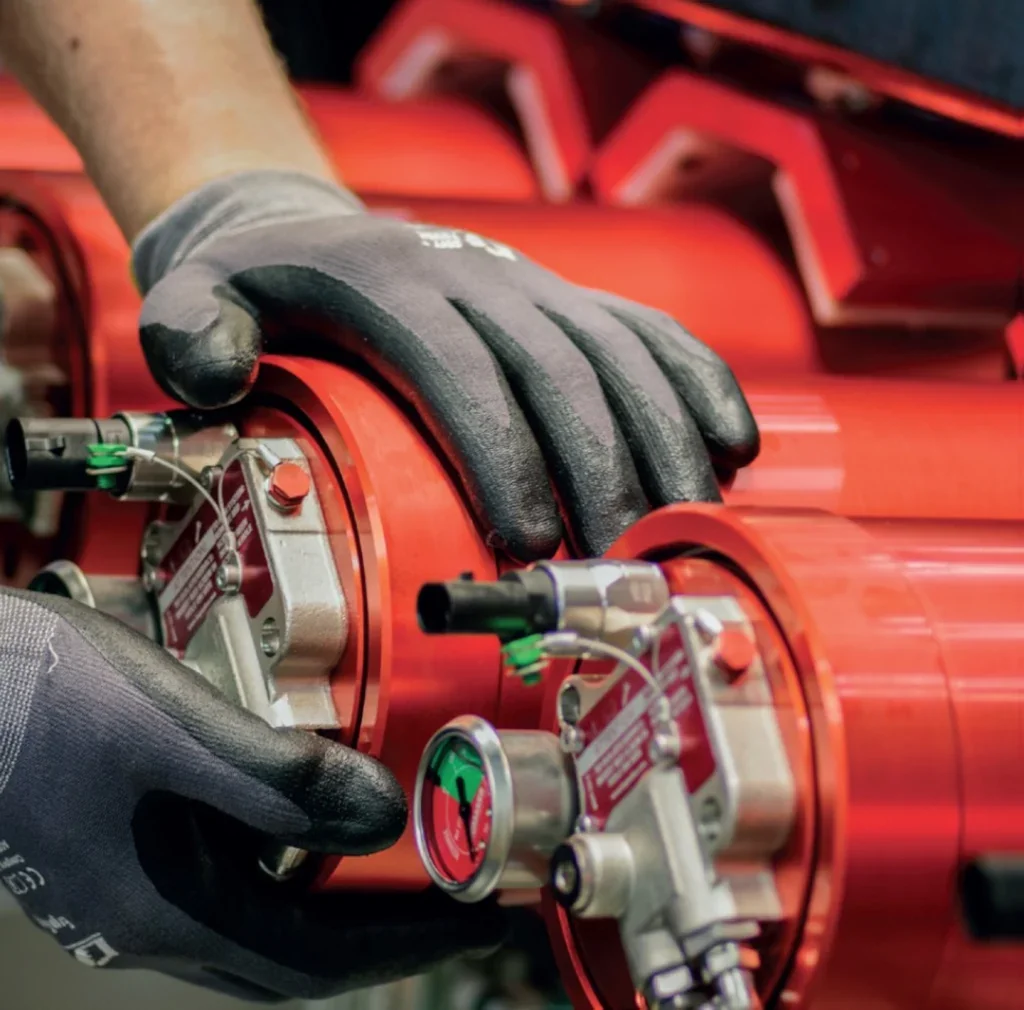
The FM 5970 Approval adds to certifications, such as the UL mark, SPCR 197 and 199, and AS 5062:2016, that the company already held for its fire suppression systems for vehicles, machines, and enclosed spaces.
The Sweden-based company develops, manufactures, and markets fire suppression systems with high-pressure water-based mist for vehicles and machines.
CEO Lars Alrutz said, in a in a statement, that the product had stood up to rigorous testing and the FM Approval would allow Fogmaker to better serve its customers in the mining segment.
He added: “This is a significant step towards achieving our vision of creating safer environments globally.”
Fogmaker has partners in more than 60 countries, two subsidiaries and over 350,000 systems installed.
Mario Flores, key account manager and responsible for the Mining, Tunnelling and Construction Equipment segment, said: “We’re not just certified, we’re approved at the highest level and verified by the most respected certification bodies in the world.”