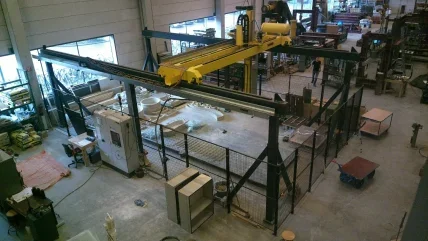
Designing segmental tunnel linings is fundamentally a process where the client’s requirements and the conditions in which the segments have to operate are assessed and a robust, compliant solution is developed. Client requirements range from elementary asks, such as demonstrating structural robustness, to specific aspects of performance, such as a maximum permitted leakage rate.
Structural design is normally undertaken within the framework set by design codes. Modern design codes such as the ACI 318, the AASHTO and the Eurocodes are based on Limit State (LS) Design where the (factored) loads need to be less than the (factored) resistance. This approach, often abbreviated as Load and Resistance Factor Design (LRFD), typically applies for the design of concrete and steel structural elements of our tunnels in Ultimate Limit State (ULS) and Serviceability Limit State (SLS). With this approach we can confidently demonstrate compliance of our designs with standard rules applied by the wider construction industry and, in turn, due professional skill and care.
The situation is slightly different for some performance requirements such as leakage rates which should be zero if our (safe and robust) design would be working exactly as designed. In the real world zero leakage is however only attainable with exceedingly robust and redundant designs and construction methods, and would be prohibitively expensive.
Staying with the example of segment gaskets, this mismatch between design and reality is often caused by imperfections of the single shell tunnel lining such as cracks, or gasket damage, or leakage around grout ports. A limited number of defects are typically not detrimental to the usefulness of the built tunnel for the asset owner, and in consequence are considered to be acceptable for a non safety-critical serviceability check. These considerations are often reflected through the selection of tunnel class by the client (following BTS Specification for Tunnelling 3rd edition, Table 16) according to its intended use, which includes a definition of the acceptable leakage always greater than zero.
The code-based design approaches typically presume that the used materials and products are regulated. Especially in segment design this is, however, not always the case – accessories such as dowels, gaskets, bicones, guiding rods, and bolt sockets are unregulated and not standardised.
THE PROBLEM
As tunnel designers we fulfil a design integration role in addition to our ‘first principles’ structural design. Every structural element we use, be it concrete, steel, wood or masonry, comes with a large package of associated material and test standards before it is deemed compliant with the requirements of the structural codes (ACI/AASHTO/EN Eurocodes). This set of standards ensures that the material performs as required in all design situations captured by the underlying code.
Such comprehensive rules do not exist for many segment accessories. While some accessories such as gaskets are backed up by detailed specific guidance (STUVA Recommendations for Gasket Frames, 2019) this is not the case for other accessories, which are typically characterised by supplier provided, product specific, data sheets.
At this point, it is useful to consider an analogy to the design of fixings. The manufacturer of a fixing will define and certify the specific performance of their product, such as tensile and shear strength, strain at failure, and specific material composition. This definition is backed up by an ISO 9001 certified assurance chain inclusive of the raw materials used in the manufacturing process.
However, the fixing manufacturer will use published standards, such as EN 1992-4 (Eurocode 2 Part 4: Design of fastenings for use in concrete), to specify the performance of their product in situ. While these values are often made accessible by the fixing manufacturer in a convenient tabulated format this does not create a responsibility for the performance of the products in situ for the manufacturer. This responsibility is shared between the constructor and the designer to interpret both the design code and the application rules, as specified by the manufacturer of the product.
For segment accessories, there typically is no design code to interpret. Parameters supplied by manufacturers are assured for the underlying series of tests and associated boundary conditions, which might differ from conditions in situ. Care is necessary to ensure assumptions made in the design are in line with the performance demonstrated in the manufacturer’s tests.
The missing link here is the lack of straightforward options for the designer to demonstrate due professional skill and care which they normally can by relying on codes or guidance, leading to a potential break in the link of assurance.
PRODUCING ADEQUATELY SAFE DESIGNS
At this point, it is useful to recap the safety concept generally underlying our designs.
Design codes such as ACI, AASHTO and the Eurocodes ultimately derive the factors applied to loads and resistances from calibration to a long experience of building tradition to ensure the design attains a code specified reliability, expressed through the Reliability Index (β) linked to the Survival Probability (PS). These are notional values, defined for the anticipated design life of the structure. To the knowledge of the author this value is ultimately derived on the basis of national experience, and its origin is not further detailed outside specialist literature. Closer examination reveals that different code families such as ACI, AASHTO and the Eurocodes largely agree in the selection of the Reliability Index.
‘Calibration against a long experience’ is typically not available for the relatively novel products used for segment accessories. An alternative way to demonstrate code compliant reliability is ‘design by testing’, with the test setup replicating the product in its installed configuration, in combination with a load representative in magnitude as well as speed of application and duration to the load the product is supposed to sustain as a minimum.
The resistance of the configuration is established from the average value of tests and the coefficient of variation. Clearly it is often beneficial to maximise the number of tests to reduce the statistical ‘jitter’. This process is described in more detail in EN 1990 Annex D and represented in ITAtech Report 7 (2016), (Guidance for Precast Fibre Reinforced Concrete Segments – Vol 1 Design Aspects) for which the author led the ITAtech Activity Group. Further guidance on setting appropriate target values for tests in an ACI/AASHTO based design can be derived from ACI 214R-11 (Guide to Evaluation of Strength test Results of Concrete).
Following this approach makes it possible to introduce non-standard elements into a fully code compliant design.
This approach is suitable for both ULS and SLS design. As specific full-scale testing is, however, relatively costly and time consuming it is often replaced or supported by numerical modelling. Care must be taken that all aspects of the numerical model are calibrated against specific tests, accurately representing the modelled parameter, in the correct time range.
Where the mechanical or chemical behaviour of products is time and/or load dependent, a prediction of the parameters over extended time periods can be difficult to make. In this case testing for the full time and load range the product is expected to work in is recommended. This typically restricts the use of such products to relatively short durations, unless verified material models for ageing can be accepted.
And, finally, it is important to remain conscious of the fact that all elements of a tunnel need to act together and the reliability requirements in consequence apply to all contributing elements to the same extent. Where it is not possible to verify the performance of a product the consequences of its failure should be assessed. A typical example would be shear elements in circle joints designed to inhibit the deformation of the lining. Where their long term effect can’t be assured the effect of their absence on gasket offset and opening should be reviewed.
FURTHER GUIDANCE
The performance of segment accessories has been subject to much attention over the last years. The STUVA (2019) specification has been a milestone for the standardised testing of segment gaskets, however its practical use has revealed some specific shortcomings.
Other segment accessories, such as bicones and dowels, remain largely unregulated. This situation is expected to improve with the release of the 4th Edition of the BTS Specification for Tunnelling (December 2023) which contains further guidance on specifying performance requirements for these important aspects of segment design, developed in collaboration with the supply chain and subjected to multiple rounds of industry-wide peer reviews.
The updated BTS Specification calls for more specific testing of segment accessories including gaskets, dowels, bicones and packers which will, in time, lead to an improved understanding of the behaviour of these elements and support data-driven design of accessories to a jointly accepted reliability level