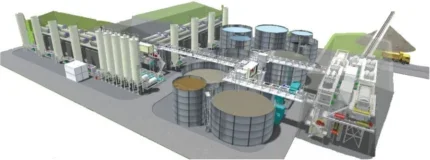
1. EXECUTIVE SUMMARY
Water, the most precious and relied upon commodity on the planet; yet despite its significance it is taken for granted. This paper follows the actions I took during my tenure at Align JV working with our supplier to launch the first full-scale testing of a polymer in the Slurry Treatment Plant (STP), the success of which has seen it produced in the UK and used as the sole treatment option across other tunnelling projects.
The paper then focuses on the development of my role as I gained interest in the next steps for the water being discharged from the STP; to lead writing the specification of a new Water Treatment Plant (WTP), taking the specification to tender, awarding and then managing the chosen sub-contractor for the new WTP. The work resulted in a new water stream being created for use and, as such, I then championed the use of this stream around the site.
Through this process, hundreds of deliveries were taken off the roads, millions of pounds saved in tankering costs and 80% of water used on site came from recycled sources, removing the reliance on the local water supply and through the treatment and reuse removing waste streams to already overworked treatment facilities.
2. INTRODUCTION
2.1. Constructions Environmental Challenges
With a growing population there is a greater need for more infrastructure capacity and increased development from an ever-decreasing resource pool, and within the context of an evolving awareness of impacts on the natural environment. Therefore, both the tunnelling and wider construction industries are receiving elevated levels of pressure to reduce their impact on the environment and resources whilst maintaining the requirement for development.
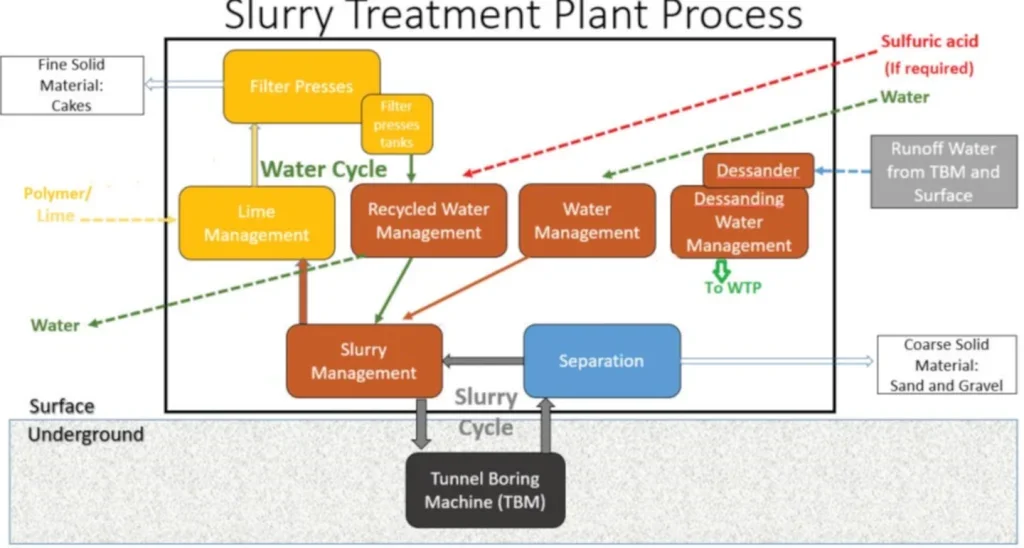
Opportunities are being realised into how to use innovation to drive the sustainability of projects as reflected by the United Nation’s (UN) Sustainable Development Goals (SDG), specifically Goal 9.
Further to this, the way project sustainability is measured is likely to change and the setpoint for standards, such as BREEAM, removing Carbon Offsetting as an option for Net Zero on projects.
“BREEAM does not recognise carbon offsets, choosing instead to focus on more meaningful reduction efforts aimed at carbon impacts associated with the construction and use of buildings,” says BRE Group.
Works need to be commenced to understand how to meet Net Zero targets by the proposed dates and enhance this to extrapolate into further changes, anticipated in future. Having said this, the recent update for the pending UK Net Zero Carbon Buildings Standard proposes to include Offsetting as a voluntary option; therefore, it will be “possible to meet the Standard with or without Offsetting,” the update said. The limits and target will remain but will use varying terminology to adhere to the UK Net Zero Carbon Buildings Standard.
In addition, there have been advancements and innovations in the testing of wastewaters; the instrumentations used for testing for contaminants are becoming more refined and are able to detect contaminants to new, lower limits with the availability of the testing to be done in a site environment instead of taken to offsite laboratories. With these technological advancements, it allows site teams and their environmental fractions to conduct tests to unprecedented levels and understand problem contaminants, like hexavalent chromium and nitrites. With increased monitoring and accountability, further action is required to ensure that the criteria are met. Note that the constraint for Align at the works, is for nitrites of up to 30 parts per billion (PPB); it is challenging to conduct tests to this level of accuracy.
Water companies are becoming increasingly pressurised through government fines and being in the public eye to tackle issues around water treatment and their untreated discharge rates. This is widely seen in various newspaper headlines in recent times. This, in turn, limits the quantities and risks that the water treatment plants will allow in their inlet waters, impacting the discharge volumes from large construction sites, and adding to the debate on the requirement for water treatment within the construction site itself. Furthermore, the water companies are proposing an increased cost to accommodate the required updates to their infrastructure to cope with current water treatment demands, reinforcing the argument that water recycling is a must for future sites.
2.2. Align JV Project
The project on which the experiences outlined in this report are to be based is the C1 Align section of HS2 Phase 1. This consists of 21.6km of high-speed rail, including the twin bore 16km-long Chiltern Tunnels, 3.37km-long Colne Valley Viaduct and associated works.
Further to this the South Portal site is to be transformed into 130ha of Calcareous Grasslands, wetland and woodland pasture habitat from a quarry and farmland ensuring a significant ecological gain for the project and assisting in the carbon reduction.
The South Portal site itself is situated within a Category 1 Source Protection Zone (SPZ1) and has a discharge permit to the River Colne via the A412 highways drainage ditch. Due to these sensitive receptors the discharge constraints for the site have to adhere to both the Drinking Water Standards (DWS) and Environmental Quality Standards (EQS) of which the key determinants are shown in the Table.
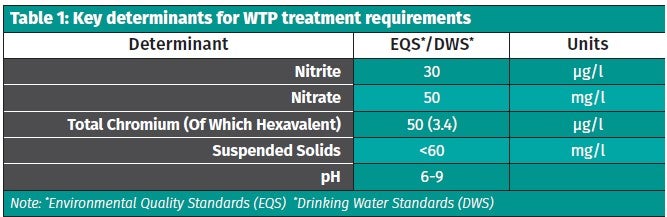
2.2.1. Slurry Treatment Plant (STP)
With the variable density tunnel boring machines (TBM) selected, an STP is a requirement to remove excavated material from the slurry and produce a ‘clean’ slurry back to the TBM for further excavation.
Figure 1 shows an STP concept model as well as a flow diagram for the process.
With the material being re-used in onsite landscaping activities ,it has been essential to control the water content of the produced spoil. To achieve this, one of the largest facilities of its kind was constructed with 24 mixed pack filter presses.
2.2.2. Water Treatment Plant (WTP)
As part of the works package, Align JV has a permit to discharge treated water offsite providing it meets set criteria, as previously stated in the Table. Initially, the WTP onsite was not sufficient to treat water to these elevated standards.
A new WTP was constructed that relies on a number of treatment steps employing hydro-cyclones, disc filters, ultra-filtration, reverse osmosis, chlorination, and granular activated carbon (GAC). The new plant also regulates pH through acid/alkali addition.
Further, the site has a waste effluent discharge permit through the sewage network and can discharge trade effluent providing it meets the levels in the licence, determined by applying a scale factor to average data values for the site.
2.3. UN Sustainable Development Goals
At the Earth Summit held in Rio de Janeiro in June 1992 the UN set out Agenda 2021, which was adopted by its 178 member states. This outlined the necessity for a global partnership for sustainable development to improve human lives and protect the environment. Over the last 30 years, at various points this has been reviewed, expanded, and amended, and in 2015 came the 2030 Agenda for Sustainable Development with the 17 SDGs, as presented in Figure 3, to provide the enabling framework to make this achievable.
Key areas where this project overlaps with the UN aims are in the following SDGs: (6) ensuring the availability and sustainable management of water and sanitation for all; (12) by actively managing sustainable consumption of the potable water supply, and reducing reliance on the trade effluent licencing; (11) through sustainable industrialisation and fostering innovation in the production methods at the site; and, (14) ensuring safe environmental discharges thus conserving the local marine environments.
2.4. Sustainability
Sustainability dates back through the ages. The rough form of its ethos is to optimise use of resource through greater awareness of how different actions can impact the local environments. Following through to the modern world, the evolution of the term can be traced to the forestry profession and its first use, in its German form of ‘nachhaltend’, where Carlowitz explains about not harvesting more than you can replant. The consideration of sustainability in forestry expanded upon work by J.Evelyn, 50 years earlier, that outlined the reduction in forestry areas and how to reverse the effects (Evelyn, 1664). This was the main use of the term ‘sustainability’ until commencement of ‘Sustainable Development’ as a thematic focus when the 1970’s began.
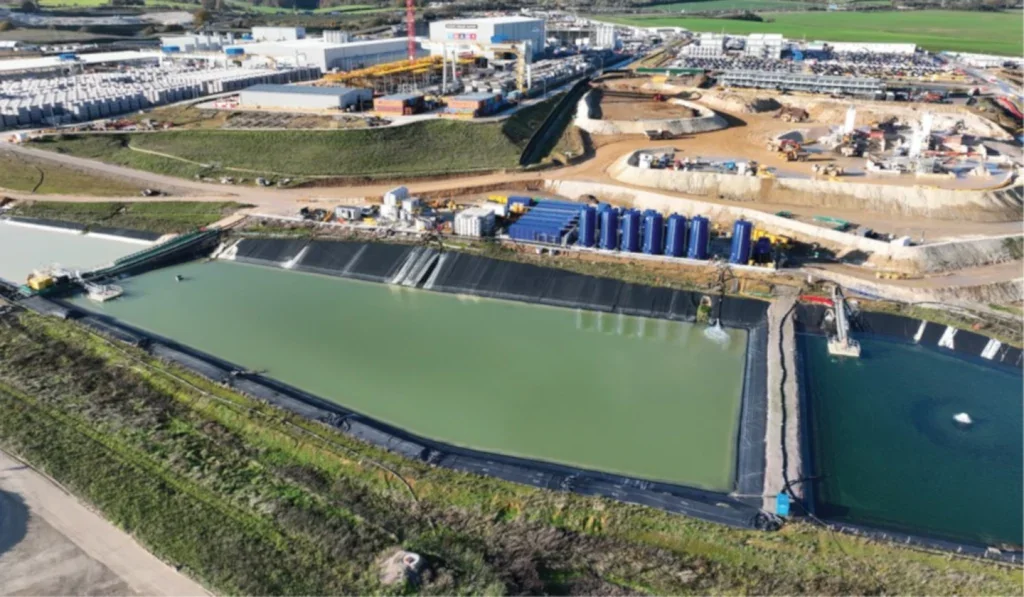
2.5. Sustainable Development History
Prior to work by the UN and the implementation of its SDG’s, ‘Sustainable Development’ was discussed and its definition is considered to be that shared by the Brundtland Report, as satisfying ‘the needs of the present without compromising the ability of future generations to meet their own needs’ (Brundtland, 1987). This definition reflected upon the work of Malthus who proposed that population and its demand of resources grows faster than the resources can recover naturally (Malthus, 1798). As a term, ‘Sustainable Development’ was coined in 1969 by the International Union for Conservation of Nature (IUCN) and then would inform the work by Brundtland.
2.6. Slurry Treatment in Construction
The review is focused to the filter pressing aspect of STPs and the generic practices before the implementation of the STP by Align.
It is well documented that filter presses can require aids to assist water from being removed from the ‘mud cake’ contained within the press. Typically, a hydrated lime is used in this process to “chemically make the slurry material release water” (McLanahan, 2019), a point reiterated by other industry competitors (Filtration and Pumping Universal Solutions, n.d.).
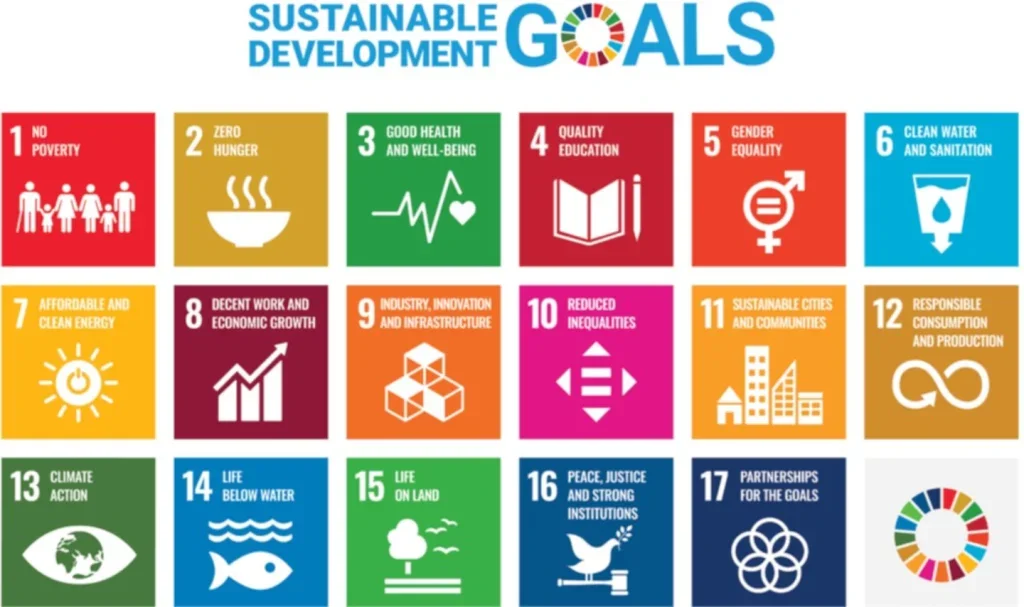
Work has been implemented to improve best practices by phasing out hydrated lime from this process due to the elevated pH and challenging reuse properties. In their work Yan Cui et al. list many benefits of using lime and explore some methods that have been identified to remove lime use, from gypsum to wood chips with varying effects (Yan Cui, 2021). However, there is little mention to either polymer tests or case studies where alternatives to lime have been used in large scale construction.
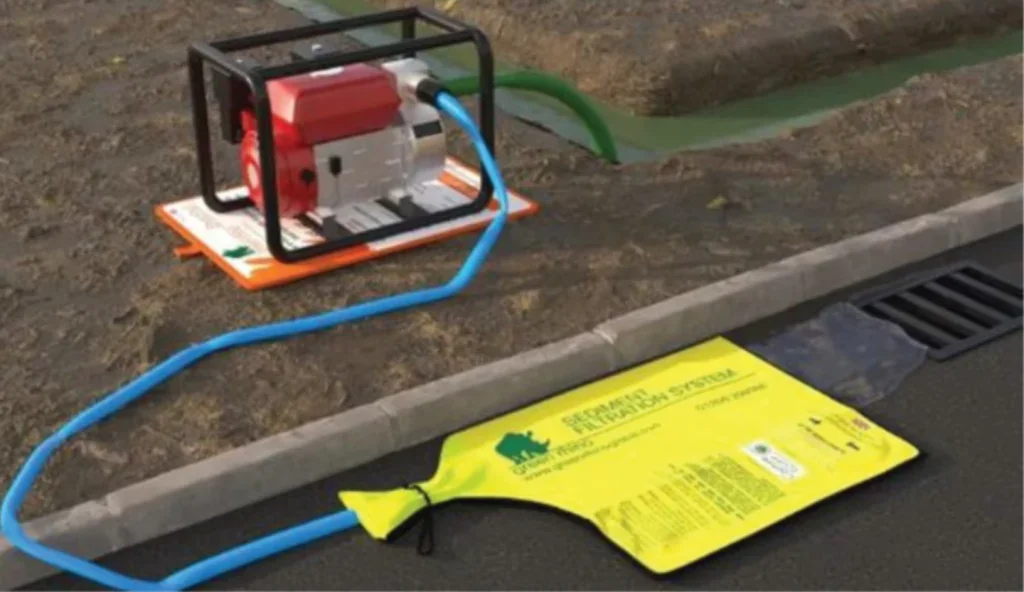
2.7. Water Treatment in Construction
Typically, in the construction environment, wastewater treatment involves removal of fines from the water course preventing blockages and to ensure pH balance of the discharged material. These treatment steps are achieved by varying levels of intervention, from mechanical filtration in straw bales through to designed water treatment plants, as discussed in the sections below.
2.7.1. Construction Projects
In conventional construction projects where the ground is disturbed and groundwater or run-off contains soil fines or dust there are small treatment solutions implemented. These treatment steps use settlement tanks or direct filtration to remove any particulate from the water course.
Proprietary systems can be used to treat and discharge the water or the steps might even involve placing straw bales in ditches to achieve the required filtration manually. Care and consideration should be taken when selecting such measures; for example, straw bales should only be considered in very short durations for, although cheap and quick to install, they have high maintenance requirements to ensure continued effectiveness (International Erosion Control Association Australasia, 2010).
Another potential solution to remove silt from wastewater can be seen in Figure 4. Such systems can also be used to target hydrocarbons and enable safe discharge to surface drains in construction projects. These are, again, quick to mobilise but require a pumping system to be available. They also require close monitoring to ensure that the filters are maintained.
Similar methodologies are used to create larger scale systems for treatment purposes in construction projects, such as settlement tanks and/or treatment systems with specific concrete washout treatment units available, an example of which can be seen in Figure 5. These can address oils, suspended solids and pH imbalance. Generally, they are provided as mobile hire units and are used in series or parallel to achieve the required water treatment targets and volumes. These systems can have sensors installed to track maintenance and productivity, in treating much larger flows, but these require space and are more expensive.
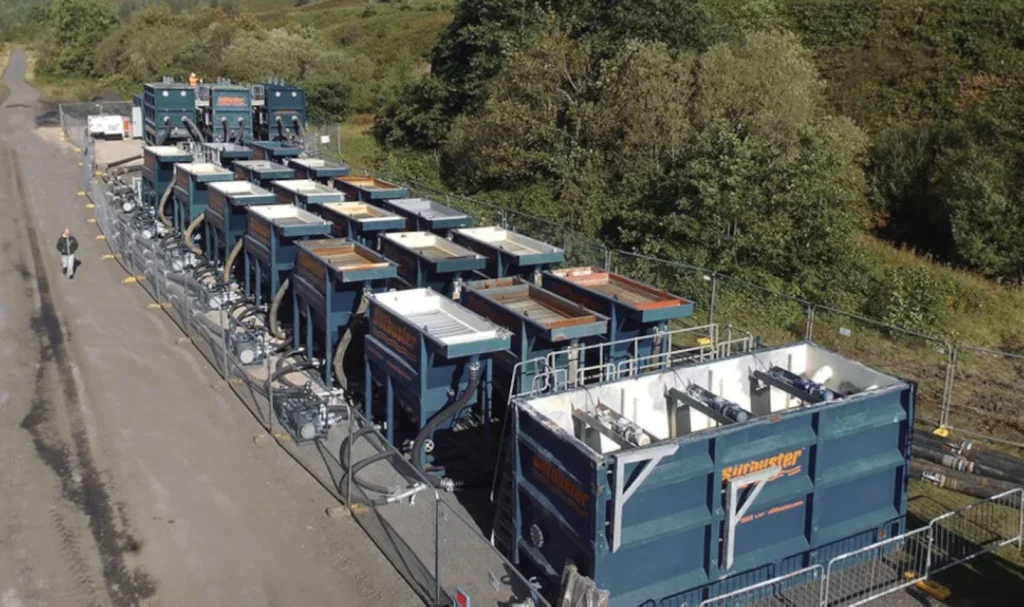
2.7.2. Mining/Tunnelling Projects
For some mining, tunnelling and piling works there is slurry generated to assist in the production processes of the works. The slurry requires treatment to allow discharge, due to the environmental constraints imposed and the quantities of slurry required for production needs.
Bespoke, larger-scale slurry operations are needed for the equipment designed for use on such works, such as TBMs. This is where STPs and WTPs are requirements.
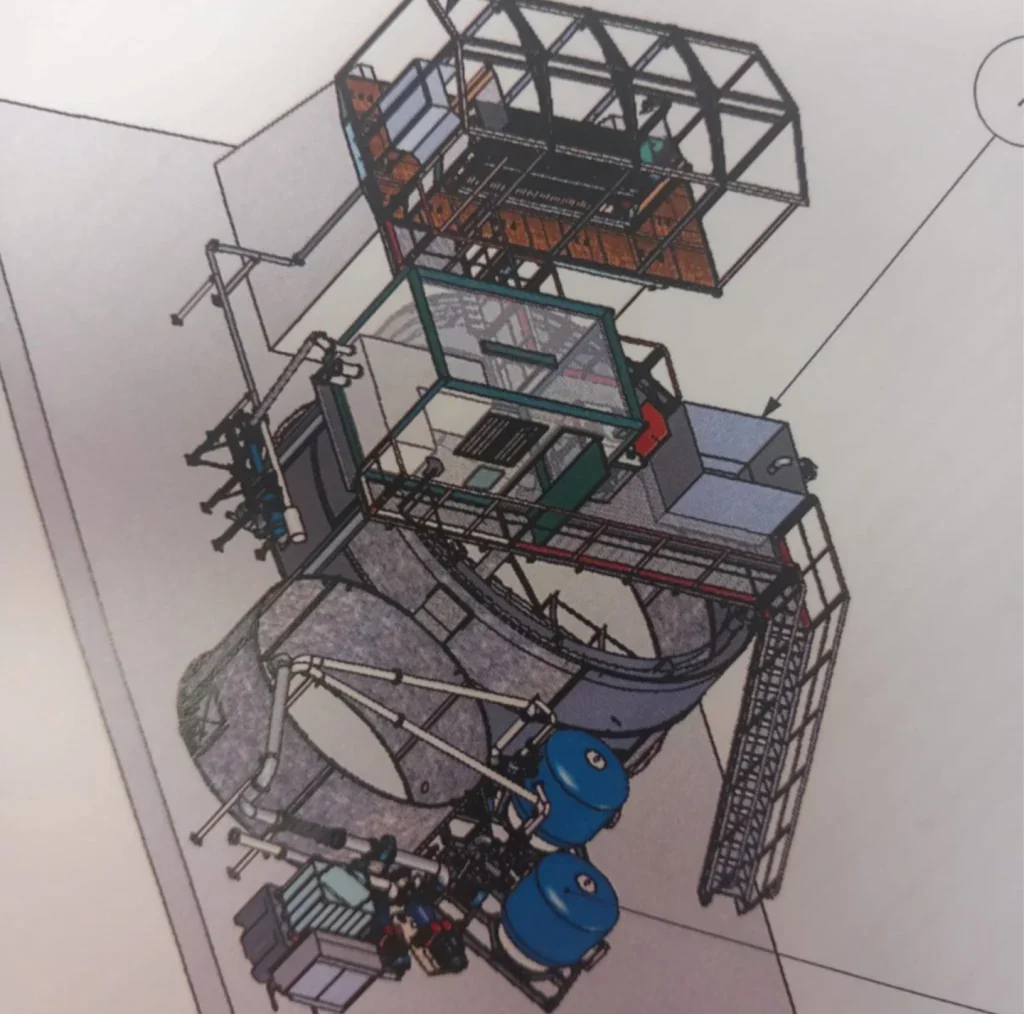
Many companies can design these facilities and there needs to be compatibility with the excavation equipment, at all interfaces of the linked system, i.e., the TBM, STP and WTP. Graphics of some of these WTP systems are shown in Figure 6, the STP graphic can be found in Figure 1.
These systems utilise specific mechanical and chemical processes to target problem contaminants and can utilise flocculation, coagulation, hydro-cyclones, filter presses, dewatering screens, centrifuges and more. These plants look at moisture contents of spoil for reuse/disposal and the problem determinants in the water for removal.
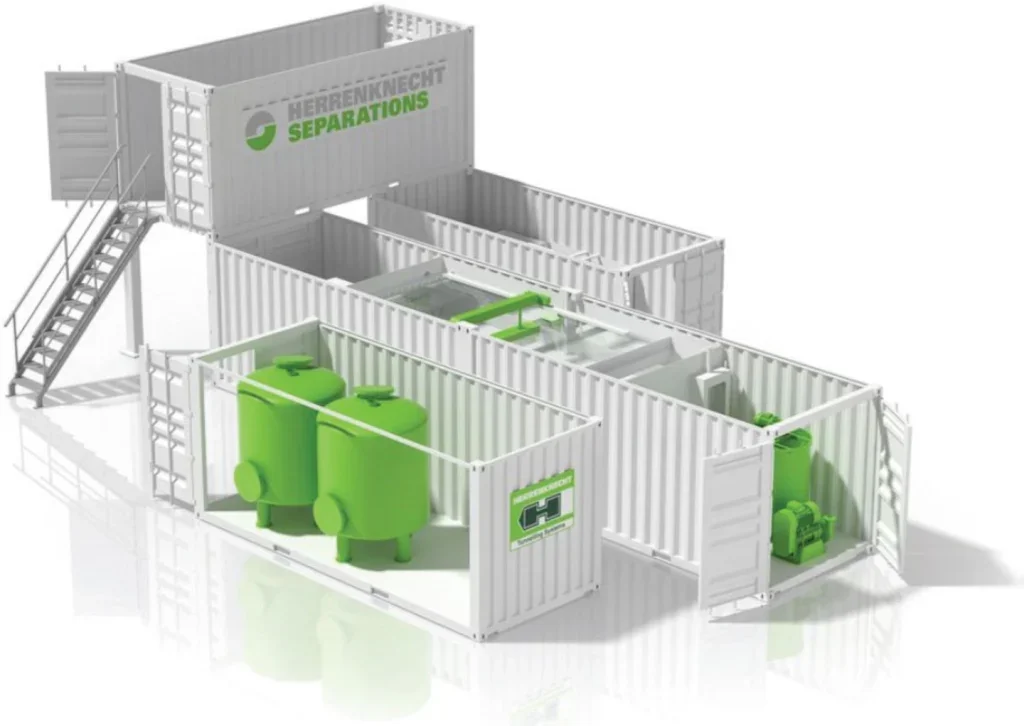
It should be noted that these slurry treatment plants and water treatment plants are modular and temporary assets by nature, mirroring a construction project’s duration; therefore, permanent plants have not been considered in this review.
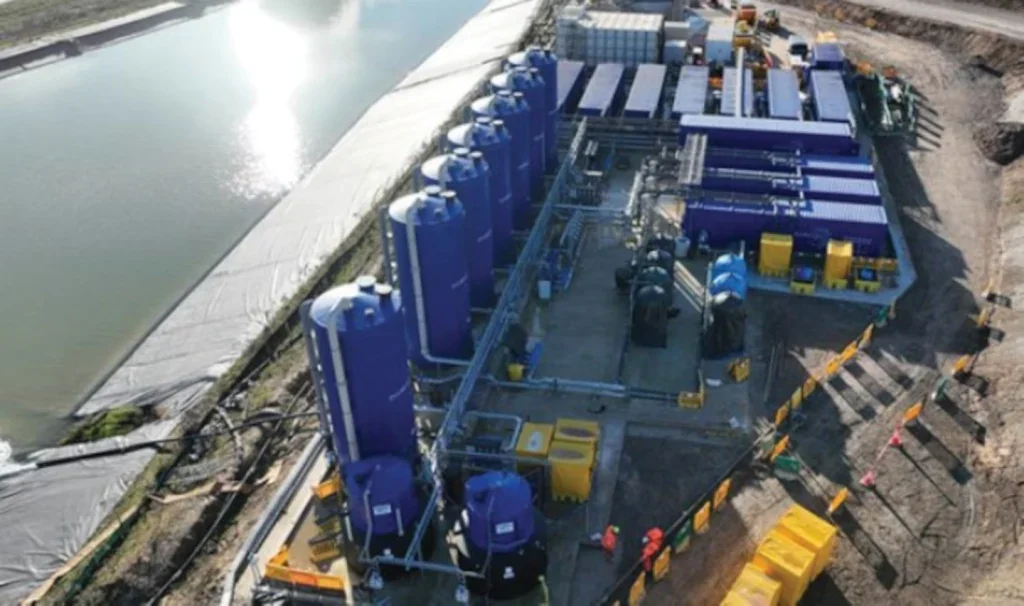
3. ROADMAP TO WATER RECYCLING
The road map for water recycling at Align followed two specific innovations: a new chemical treatment at the STP; and, a bespoke plant at the WTP.
In the following sections, the paper sets out the four main phases of works that were associated with these two innovations chronologically and also my involvement in achieving these works.
- Moving from Hydrated lime to a polymer at the STP Filter press
- Dismissal of the pre-operational condition within the Wastewater Discharge Consent
- WTP trials and new WTP
- Water Recycling
The final section will then explore the benefits that have been realised by the recycling network and how this has directly impacted the sustainability for the project, and, further, how it can impact the future of tunnelling construction.
3.1. Innovation 1 – Polymer in the Filter Press
At the commencement of the project, the STP had been set up to initially use the standard treatment chemicals of hydrated lime and sulphuric acid in the filter press process; there was an option to use a polymer to optimise the process. This removed high pH byproducts, extra site deliveries and reduced the amount of exposure and handling, and so improved management of the environmental and safety hazards.
If continued to be used then 17,500 tonnes of lime would be needed, producing 4.5 million tonnes of filtrate water at pH 12 that would need treatment using 8,400 tonnes of sulphuric acid. The alternative option would see 4,600 tonne of polymer used and that would generate the 4.5 million tonnes of filtrate water ready for reuse at pH 8.
Previous filter press tests had been commissioned by STP manufacturer, MS. However, those tests were carried out within different geology, used bentonite, additional flocculants, and were undertaken with different polymers. Further, this project would also be the first full industrial-scale application.
As the STP Engineer for the project, I was responsible for championing the investigation of this polymer in the filter press with the STP manufacturer, through the STP production teams. Additional work had been done by the supplier ahead of the on-site trials to determine the best polymer to use – FLOPAM MS PRESS 3 – and the dosage rates to trial.
The STP circuit had been operated in ‘closed loop’ to the trial and contaminant build up from this phase needed removal by flushing the slurry system, undertaken by draining the filtrate water tanks to the WTP ponds and diluting the excavated slurry with fresh water during production.
I worked with the authorising body, the EA, during this time to get the required approvals to discharge a volume of water to the pond system. The trial overlapped with this phase prior to ensure no adverse effect on the data by running in ‘closed loop’ and concentrating any potential contaminants within the system. The system was returned to ‘closed loop’ for a section of production and the sample suite repeated for comparison. During these works, various samples were taken throughout with a mixture of in-situ tests, inhouse laboratory tests and external chemical suite analysis.
At completion of the polymer trial, the plant was then switched back to lime and the testing regime was rerun for a base comparison.
The conclusion for the testing revealed that the polymer is a comparable replacement for lime in a productivity sense with many added environmental and health and safety benefits. A leachate report was also undertaken to analyse the long-term effects in the chalk cake; and works were initiated to allow use of the polymer exhaustively.
During this process I monitored the STP performance through a variety of reports and observations. I orchestrated the testing regime and provided the key logistics to ensure that the samples taken were transported to their respective laboratories in the correct conditions.
3.2. Wastewater Discharge Consent
Included within the pre-operational conditions of the sites Environmental Consent was a specific requirement around the suitability of the polymer. To discharge this polymer, a Compliance Assessment Report (CAR) was needed, consisting of the three trial documents. One of the reports was on the physical assessment of the trial that I authored, and collated the information from the trial and resulting test data, and others by my colleagues on the chalk leachate and filtrate water discharge quality.
This process then ignited many conversations upon which various stakeholders were invited to the site. I then embarked on touring the STP to show firsthand the potential benefits of the polymer, large scale application and the efforts to make the project as sustainable as possible.
The results of the report submission and the following engagement visits resulted in the acceptance of the CAR, thus allowing process water treated at the STP to be discharged to the Water Treatment Plant.
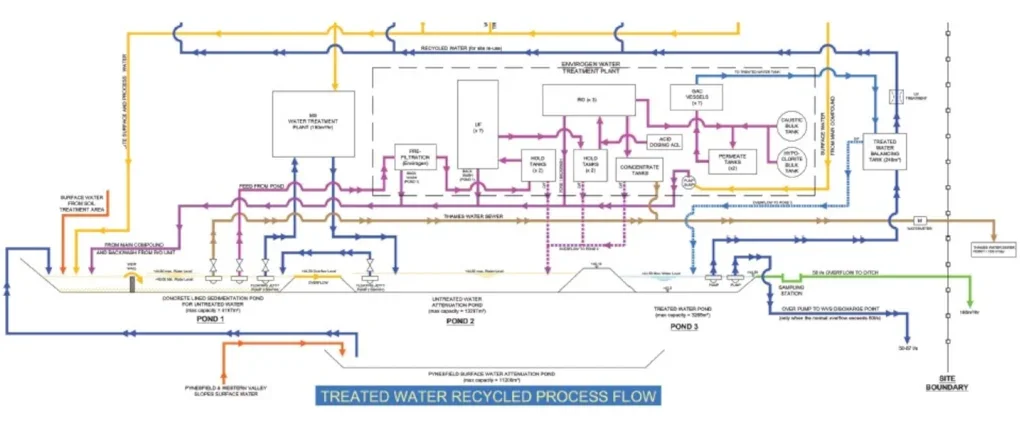
This was a vital stage in allowing the innovation to be replicated across other HS2 sites and also in the recycled water initiative at Align, enabling the JV to move and treat the water further. It has added a host of other opportunities as well as being self-reliant through the environmental discharge permit.
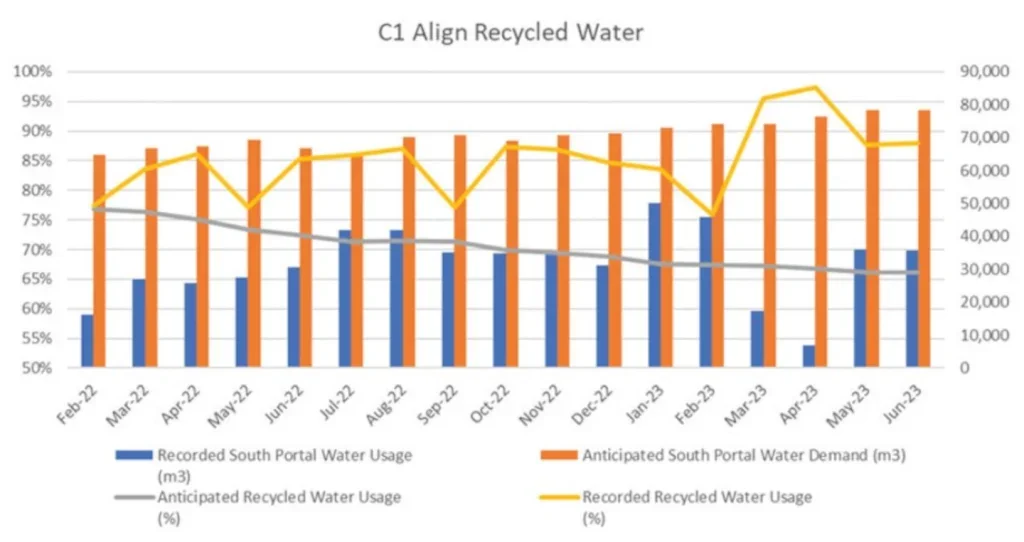
3.3 Innovation 2 – New WTP
The success of the above report, stakeholder engagement and production works at the STP led to an expansion of my interests as to the next steps for the water treatment process. From this interest I also expanded my role to incorporate the WTP.
The original WTP at Align could treat for pH correction and removal of suspended solids, although not meeting the stringent requirements for discharge to the environment as detailed in the Table.
Initially, a series of on-site trials were undertaken, primarily using a reverse osmosis (RO) container to further treat the original WTP discharge. This successfully removed most contaminants but raised the pH. Changes were made to reduce the pH through the original WTP and add oxygenation methods to the treated water storage pond to remove the nitrites to acceptable levels. However, the oxygenation wasn’t realised and therefore an ion exchange unit was added to the RO, which successfully treated the water to the required quality for discharge. I was involved throughout this trial-and-error approach as the production lead, exploring the technical possibilities with different subcontractors, liaising with the onsite environmental team and a specialist consultant.
With the concept proven, it was then needed to be established at production scale. While following the trials, I had built up a portfolio of information and so I volunteered to produce a specification for a new WTP, capable of meeting the discharge criteria (including waste feed to sewer) based on the measured inlet water quality measured on site. This was to accommodate both – water from production activities and the anticipated surface water run-off from rainfall events.
From this work, I then presented the package to various potential bidders taking the specification to tender through enquiries and to contract award. This gave me insight into the commercial and contractual requirements at the early inception of construction. I then worked with the chosen subcontractor, vesting the materials on a fortnightly basis to secure a cashflow prior to the overseeing of both factory and on-site acceptance tests. The timescale for the project was a key consideration in awarding the contract and the plant went from tender award to treating water in under six months.
The installation of this plant, pictured in Figure 7, has allowed Align to treat water at 250m3/hr to the quality parameters required for discharge. This means the plant can discharge all site water to the environment, bypassing the reliance on a public sewage treatment works. Due to the stringent environmental constraints, the water produced from the project is of such a high quality that there was a potential to be reused on site. This would alleviate the requirement on the potable water network thus securing sustainable consumption and production, and thereby reducing impact on water availability for local inhabitants achieving SDG’s 6 and 12 in the process.
3.4. Water Recycling
At the outset, site recycled water was considered an important factor for optimisation and efficiency. A storage tank was installed at the WTP connected to a pressurised main running throughout the site, as seen in the process flow diagram on Figure 8. However, due to the length of time passed between its installation to the point of use, methods had already been standardised and the network was then seldom in use.
Here, I used the installation drawings to track where the connections surfaced, which allowed me to champion the use of the water for tunnel cooling and the batching plants. This work led to three new connections being made in the pressurised main network to support cleaning of the concrete MSVs and for use in the batching plants.
I monitored all points of the recycled network and its potable counterparts, taking regular readings from production aspects across the project, including, but not limited to, concrete batching, the tunnel segment precast factory, STP, WTP, tunnel works and TBM production, and dust suppression. With these datasets collected, I compared them to the calculations for water consumption made at the outset of the project, shown in Figure 9. These innovations vastly reduced the reliance on the potable water network; the recycled water on average provided 85% of the water consumption.
It should be noted that these recycled water figures were achieved despite running the plant in a suboptimal way for production. The plant had to be run to maintain a low water level in the pond storage network, generating capacity against rainfall scenarios. In retrospect, it would have been beneficial to run the plant to accommodate demand for the recycled water thus preventing overflows to environment close to predicted dry spells, reducing the recycled resource.
4. CONCLUSIONS
Through my own works at site on the Align project, delivering the Chiltern Tunnels and Colne Valley Viaduct for HS2, it has been possible to implement and optimise a site-wide water recycling network. This was achieved using the strict environmental discharge constraints, and having sufficient water to use in wheel washers and also dust suppression on sensitive ground within a Category 1 Source Protection Zone (SPZ1). This water source has also been used for production activities including the tunnels cooling water network and supplies into the concrete batching plants.
This recycling initiative, in turn with the reuse of water at the STP, reduced potable water demand to less than 15% of the total site requirements. The initiative directly correlated with the UN SDG’s 6, 9, 11, 12, 14 & 15. This paper also delivers toward SDG 17, using the partnerships formed through the BTS network to share experiences and the possibilities achieved for water treatment, discharge and recycling within large scale construction thus ensuring its implementation across other projects. This will help to ensure that tunnelling remains at the forefront of innovation, improving its sustainability for future projects and gaining the benefits of being self-functioning, including removing the reliance on other industries and infrastructure.
To rephrase Coleridge’s words from the Rime of the Ancient Mariner “Water, water, everywhere, Nor any drop to drink”, (1798) I think a better use now would be ‘Water, water, everywhere, How to reuse, let’s think!”
REFERENCES
- BRE Group. (2023, 07 12). ‘Building an effective net zero strategy with BREEAM.’ Retrieved from https://bregroup.com/insights/building-an-effective-net-zero-strategy-with-breeam/
- Broz, B. (2017, 05). ‘Controlling Runoff and Erosion at Urban Construction Sites.’ Retrieved from Extension University of Missouri: https://extension.missouri.edu/publications/g1509
- Brundtland, G. H. (1987). ‘Our Common Future.’ Oslo: World Commission on Environment and Development
- Carlowitz, H. C. (1713). ‘Sylvicultura oeconomica.’ Legare Street Press (26 Oct. 2022)
- Clemence-Jackson, K. (2023, 12 15). ‘UK NZCBS Winter 23 Update.’ Retrieved from UK Net Zero Carbon Buildinggs Standard: https://www.nzcbuildings.co.uk/_files/ugd/6ea7ba_32905de5d6fd42bc83b207f17af9ec29.pdf
- Coleridge, S. T. (1798). ‘The Rime of the Ancyent Marinere.’ Dover Publications (1970)
- Evelyn, J. (1664). ‘Sylva, or A Discourse of Forest-Trees and the Propogation of Timber in His Majesty’s Dominions.’ London: Royal Society
- Filtration and Pumping Universal Solutions. (n.d.). ‘Sludge Press Conditioning.’ Retrieved from Filtration and Pumping Universal Solutions: https://automaticfilterpress.com/sludgeconditioning
- Green Rhino. (2023, 08 22). ‘Sediment Control on Construction Sites.’ Retrieved from Green Rhino Global Blog: https://greenrhinoglobal.com/blog/sediment-control-on-construction-sites
- Herrenknecht. (2024, 12). ‘Technologies for Unrestrained Performance.’ Retrieved from Herrenknecht Separations: https://www.herrenknecht-separations.com/en/translate-toenglish-produkte#c235
- International Erosion Control Association Australasia. (2010, 04). ‘Straw Bale Barriers.’ Retrieved from IECA: https://www.austieca.com.au/documents/item/273
- Malthus, T. (1798). ‘An Essay on the Principle of Population.’ London: J.Johnson
- McLanahan. (2019, 08 15). ‘Filter Press Cycle Time.’ Retrieved from McLanahan: https://www.mclanahan.com/blog/8-factors-affecting-filter-press-cycle-time
- Ofwat. (2024, 08 06). ‘Thames, Yorkshire and Northumbrian Water face £168 million penalty following sewage investigation.’ Retrieved from Offwat: https://www.ofwat.gov.uk/thamesyorkshire-and-northumbrian-water-face-168-million-penalty-following-sewage-investigation
- Siltbuster. (2024). ‘Infrastructure.’ Retrieved from Siltbuster Water Quality Matters: https:// www.siltbuster.co.uk/sectors/infrastructure
- Sustainability for all. (n.d.). ‘Do you know when sustainability first appeared?’ Retrieved from Sustainability for all: https://www.activesustainability.com/sustainable-development/do-you-know-when-sustainability-first-appeared/
- United Nations. (2023). ‘United Nations Department of Economic and Social Affairs Sustainable Development.’ Retrieved from ‘The 17 Goals’: https://sdgs.un.org/goals
- Yan Cui, W. Z. (2021). ‘The role of lime in dredged mud dewatered by a plate and frame filter press and potential substitutes.’ Environmental Science and Pollution Research, 28, 17331-17342.