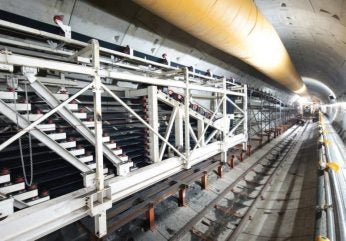
In the Philippines, the capital city is investing in a major underground expansion of its transportation system. Manila’s aim, in undertaking the large-scale civil engineering works, is to vastly improve the urban commuter network. The target date for Manila’s metro system to open is now 2028-29.
The Department of Transportation (DoTr) is developing the project – Metro Manila Subway Project (MMSP) – which is the country’s first mainly underground railway system.
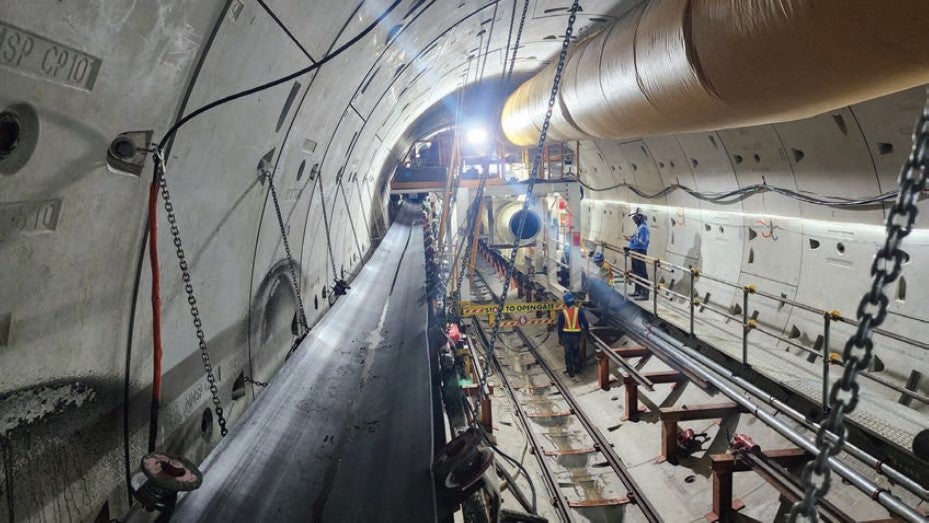
The 33.5km-long mostly underground subway line will run from Mindanao Avenue, in Valenzuela City at the north end of the route and via a number of intervening stations it will link with Western Bicutan, in Pasay City at the southern end. The MMSP line will have a spur at the Ninoy Aquino International Airport.
Contract Package (CP) 101 – CP 101 – is at the northern end of the MMSP. The lot was awarded to a Japanese joint venture of Shimizu Corp, Fujita Corp, Takenaka Civil Engineering & Construction Co, and EEI Corp. The early works are supported by Japan’s development agency, Japan International Cooperation Agency (JICA), which just over two years ago signed a 40-year loan (13-year grace period) for approx US$1.65 billion and under the terms also brings involvement of Japanese tunnelling technology.
JICA has also, separately, provided funding support for rehabilitation works on Manila’s existing Metro Rail Transit Line 3 (MRT3) to improve safety and service performance on the light rail, mostly surface link that also will have a portion of tunnel works, the agency said in a release last year.
On the mainly underground MMSP, the CP101 lot is composed of a Subway Depot at Valenzuela City end and then the alignment runs southward below the surface to three stations – Quirino Highway, Tandang Sora and North Avenue, on the end of the lot.
The client said in early March, during the launch of TBM-4 at North Avenue station, that the package was 40% complete and it expects the section to open for partial operations by 2029.
But the client added that finishing on schedule would mostly depend on resolving right-of-way issues – such as demolition for station works as well as some property owners concerned over tunnels passing below their buildings. Efforts are underway to resolve the problem, trying to convince property owners that project plans have accounted for the building structures as parts of design and construction planning.
CP101 is one of seven civils works packages on the entire project.
Japanese consultancy services to the lot have been provided by OC Global.
The Japanese JV contractor is receiving tunnelling equipment for the lot as six TBMs via the Japanese company JIM Technology (JIMT), which has a stake in Terratec, plus conveyors from Terratec.
JIMT was formed in 2016 through the merger of the tunnel excavation businesses if IHI Corp. JFE Engineering Corp, and Mitsubishi Heavy Industries.
The TBMs are 6.99m-diameter earth pressure balance (EPB) machines. JIMT says the cutter power of each machines is 924kW, torque is 6307kNm, and effective thrust is 48,000kN. Geology along the alignment consists of sandstone. Siltstone, gravel, boulders, clayey sand, silty sand, clayey/inorganic silts, and sand and gravel both poorly graded.
Working in pairs, the parallel TBM drives on the lot are: 2 x 1509m; 2 x 1458m; and, 2 x 1780m.
The two Terratec Continuously Advancing Conveyors that have been supplies are to play a vital role in the construction of the first, and most northern, portion of CP 101, between the Subway Depot and Quirino Highway. Matching the lengths of the first of the listed parallel TBM drives, the conveyors are each 1509m in length. They have single pulley head drives of 150kW and are able to operate at a rate of 225m3/h, handling the various materials during mucking out along the entire length of each belt. They can transport sandy gravel and boulders up to 400mm in size.
The tunnel conveyors are equipped with electric drives that have electronic Variable Voltage Variable Frequency (VVVF) controllers for each motor to help deliver smooth starting, load sharing, and precise control.
Hydraulic tensioning of the conveyor belt system is employed for horizontal cassettes to enable accurate take-up tensions and reliable control. The widerthan- standard carry and return roller sets allow for enhanced belt wander tolerance and improved control in horizontal curves, says Terratec. Two-roll vee-return idlers are utilised throughout for proper return belt tracking.
Terratec’s patented design of the Advancing Tail Piece levels the conveyors using an active hydraulic system to match the steering/ rolling position of the TBM, which enables horizontal and vertical curves to be negotiated smoothly.
The conveyors are designed to handle both steady state and unsteady conditions, including acceleration, controlled deceleration, and unpowered stopping for loaded and empty conditions.