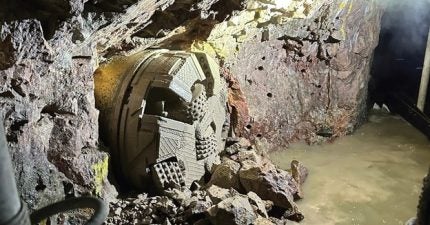
The need for new drinking water and sewage lines is huge. And around the world it will continue to grow. Apart from the costs, this increasingly poses a specific problem: in many places, space underground is becoming scarce. To avoid impairing existing infrastructure, new lines have to be installed at ever deeper levels. This often also means in places with greater geological demands. And, last but not least, the installation of new underground pipelines also entails enormous logistical difficulties on the surface, especially since, by its very nature, it usually takes place in densely populated areas.
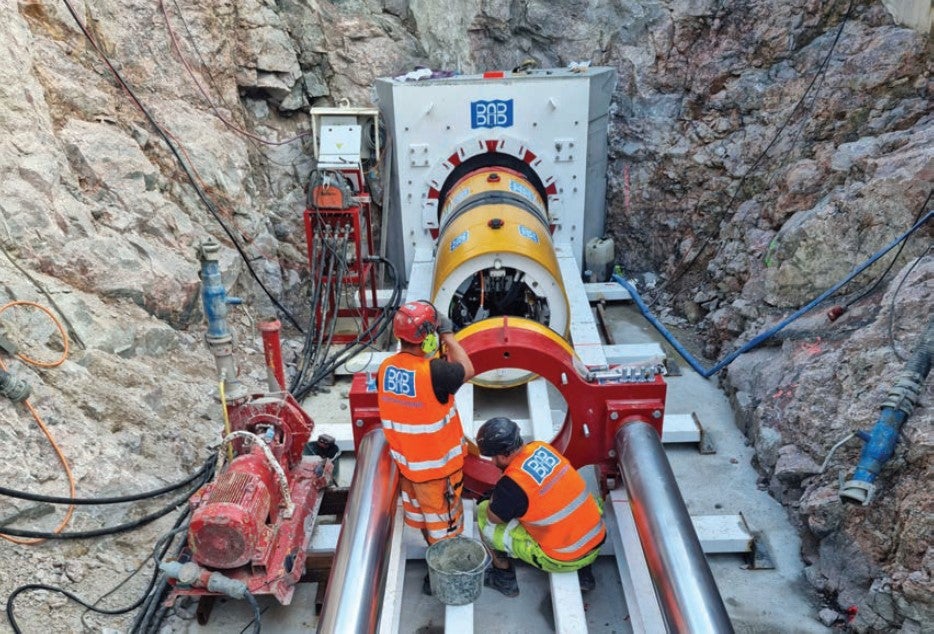
MICROTUNNELLING: SPECIFIC ADVANTAGES AND DISADVANTAGES
Against this background, trenchless excavation with remote-controlled microtunnel boring machines (MTBM) offers major advantages: for one thing, it can be carried out very precisely. Particularly in the case of gravity flow pipelines, this is essential to ensure the required accuracy in terms of height and position. The exact routing also means that other underground infrastructure can be taken into account and safely bypassed. On the other hand, spatial and acoustic impairments for people and traffic as well as the impact on the building fabric on the surface are reduced to a minimum. And, microtunnelling is generally more cost-effective overall than the conventional open-cut method.
Accordingly, microtunnelling is used successfully around the world for driving water and sewage lines, but also, for example, service tunnels or protective tunnels for pipelines with diameters of up to 4m.
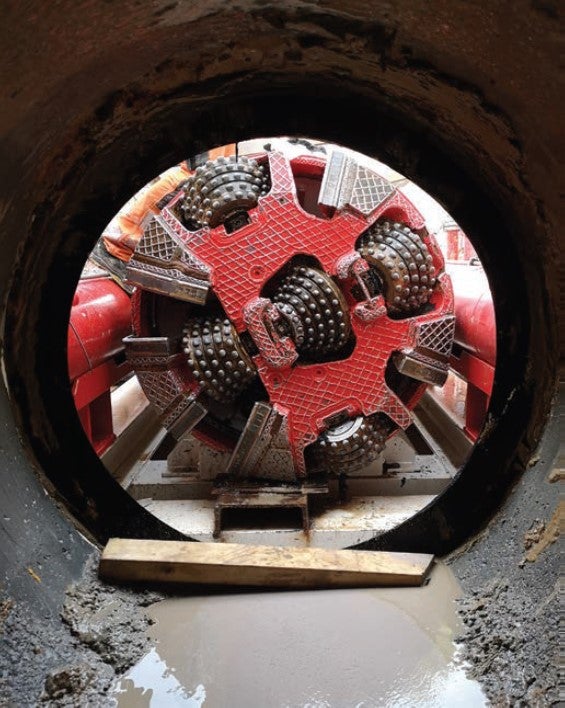
These advantages are, however, offset by specific technical challenges: with internal diameters of less than 1.20m, people are not allowed to enter the tunnel. This usually means tool changes underground are not possible. The aim in developing appropriate tunnelling systems and tools is, therefore, to be able to achieve the longest possible drive distances without tool changes. This minimises the number of shafts and their costly and time-consuming construction. This applies all the more to complex ground such as hard rock. The harder the ground, the greater the wear on the cutting tools.
DRILLING IN HARD ROCK: TUNNEL PROJECT IN SOLLENTUNAEDSBERG
The planners of Johan Lundberg AB and construction team of BAB Rörtryckning AB on a utility project north of Stockholm, in Edsberg in the municipality of Sollentuna, also had to deal with particularly complex hard rock. The geology is mainly granite and gneiss. The uniaxial compressive strength (UCS) ranges from 128MPa to 248MPa (average: 174 MPa) with a tensile strength of 9.9MPa to 16.9MPa (average: 14.3MPa). The abrasiveness is also very high with an average Cerchar Abrasivity Index (CAI) of 4.5 (CAI 4.1 – 4.7). The average RQD (Rock Quality Designation) is 95 (RQD 90 – 100). Or to put it plainly: this is literally biting on granite.
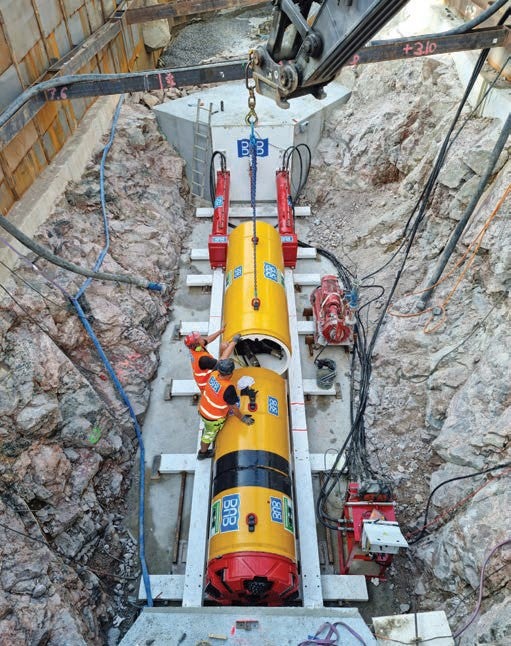
A new sewer tunnel with a drive length of 163m and a shield diameter of 1110mm thus had to be excavated in these extreme ground conditions. A low slope with a longitudinal inclination of 5.9 ‰ and with an overburden of between 5m and 15m, it runs in a straight line to the so-called Käppala Tunnel, into which it opens directly. Built in the 1960s, the Käppala Tunnel connects to the sewage treatment plant of the same name in Lidingö. It is the third largest in the country and treats the sewage of around 500,000 people in 11 municipalities in the north and east of the Swedish capital.
The underlying geological conditions initially seemed to favour classic drill and blast or a pneumatic hammer. For a number of reasons, however, in this case these conventional approaches were ruled out. Firstly, they do not offer the required precision, in particular at the confluence with the existing sewer. The challenge: this was not allowed to be damaged or affected with an additional high amount of water flow that would come from alternative raise drilling method. Secondly, the historic rococo style Edsberg Castle and its park are situated in the immediate vicinity of the jobsite. The tunnellers were thus faced with the task of protecting the valuable building fabric from damaging vibrations and avoiding noise and dust as far as possible.
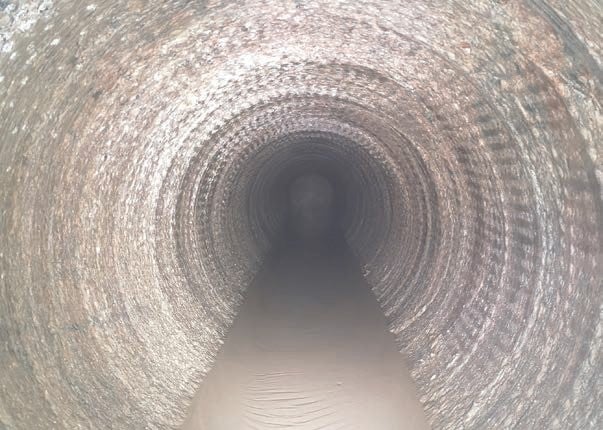
The only alternative was therefore an actively steerable MTBM. However, this not only had to cope with the hard, abrasive rock on site but it also meet other exceptional requirements: as the new tunnel was to run directly into the Käppala Tunnel, no shaft would be possible at the reception point to recover the machine after breakthrough. The situation with regard to buildings on the surface also meant an intermediate shaft was not an option. This meant the machine had to be able to be pulled back to the launch shaft both for the final recovery and for any tool changes during the drive.
COLLABORATING FOR GREATER SUCCESS
It quickly became clear that no such machine existed (yet) on the global market. So planner Johan Lundberg AB and contractor BAB Rörtryckning AB, working closely with German TBM manufacturer Herrenknecht AG, set out to find a solution.
Jan Wandeby, project designer and construction manager, Johan Lundberg AB, describes the situation: “When we started the planning process, we investigated several alternatives but couldn’t find a feasible solution. After many years of planning microtunneling (MT) projects within our company – we were the first in Sweden to be planning MT projects – we had already established a good relationship with Herrenknecht. The excellent collaboration with Herrenknecht has been crucial for this work since they were able to produce a machine that could complete the drill according to the conditions at hand.”
The result of the collaboration is a world first. The key element of the solution ultimately realised was using flangeable steel pipes as jacking pipes. Using these temporary pipes, the machine can be retracted. It proved helpful that Herrenknecht already had in its portfolio a smaller microtunnel boring machine with active steering for smaller applications with an outer diameter of 960mm. A revised version of the machine was required, which on the one hand is designed for slightly larger outer pipe diameters of approx. 1100mm, and on the other is able to handle the jacking and removal of the temporary steel pipe. The result of the joint project planning phase was the remote-controlled AVN 800 HR microtunnel boring machine for pipejacking in hard rock (“HR” for “hard rock”).
HERRENKNECHT’S NEW AVN 800 HR
The newly developed AVN 800 HR is based on Herrenknecht’s proven AVN technology. ‘AVN’ is the abbreviation of the German for ‘Automatic Tunnel Boring Machine Wet Conveying’ and stands for the slurrysupported removal of material, the so-called slurry method. The machine mixes the material removed from the face with water in a closed circuit. The slurry with cuttings is pumped to the surface where it is separated. That is, the excavated material is separated from the slurry. The slurry can then be fed back into the water circuit and the excavated material transported away.
AVN machines are closed full-face tunnelling machines with a closed hydraulic slurry circuit. The ground ahead is excavated with a cutterhead adapted to the geological conditions. Parallel to the advance, a tapered cone crusher in the excavation chamber crushes the excavated soil and stones to conveyable grain sizes. The material then falls through sieve-like openings in the cone crusher and is sucked out with the suspension via pumps through the slurry lines. The excavation diameter can be flexibly enlarged using an extension kit and an adapted cutterhead. This means that different diameters within a certain range can be realised with one AVN machine.
The AVN machine series offers a wide range of options for both pipejacking and segmental lining as well as for all types of ground conditions: from silt and clay to non-cohesive soils and gravel through to rock. Standard or mixed soil cutterheads are used in soft soils and mixed geologies. A rock cutterhead with disc cutters is installed for drives in solid rock.
Previously, however, the hardness limit for AVN machines in non-accessible dimensions (i.e., with an inner diameter of less than 1.20m) was around UCS: 50MPa to 80MPa – too low for the abrasive hard rock in Edsberg, with a UCS of up to 248MPa. The Herrenknecht engineers therefore looked for – and found – optimisation potential for the AVN 800 HR in two areas in particular: the cutting wheel and the main bearing, respectively.
INNOVATIVE CUTTING WHEEL DESIGN WITH TCI ROLLER BITS
The cutting wheel design is characterised by particularly wear-resistant raise boring cutters with tungsten carbide (TCI).
The tooling of the cutting wheel is the most important element in rock applications. The size and arrangement of the tools are determined on the basis of the rock properties in order to obtain the conveyable chip size of the rock pieces that can be processed by the conveyor system.
In addition to TCI roller bits for hard rock, there are two main types of cutting tools that can be used for MTBMs: disc cutters or toothed roller bits.
The most commonly used are still the classic disc cutters known from large-diameter hard rock TBMs. For space reasons, the disc cutters are usually equipped with double or triple cutting rings, which reduces the distance between them and allows the rock to be reliably crushed. In addition, the larger number of rings on the discs reduces the available contact force per ring and therefore the likelihood of tensile cracks occurring, which lead to chipping or spalling. It is therefore important that small-diameter AVN machines for hard rock have a high jacking force and strong main and disc cutter bearings.
If this problem cannot be solved technically or if high demands are placed on the service life of the cutting tools, TCI roller bits, as used in the AVN 800 HR, are the best choice. TCI roller bits apply selective force to the rock, creating many small chips. Due to the tungsten carbide insert, the TCI roller bit is extremely wearresistant.
As an additional innovation, the AVN 800 HR has a particularly strong main bearing for high contact forces. The maximum contact force is 890kN (89 t) – around three times as much as the standard version AVN 800A. A flushing ring at the bottom of the machine with a remote-controlled ball valve additionally keeps the contact forces low by preventing fine rock particles from penetrating the annular gap. At up to 26 rpm (at 260 l/min), the revolution of the cutting head is in fact four times higher than the standard version, which increases the maximum advance speed in hard rock to up to 25 mm/min and more, thus enabling a cost-effective advance. As a result, the AVN 800 HR can achieve drive lengths of up to 200m (depending on rock specifications) without the need for a tool change. This is twice as much as the AVN 800.
Johan Lundberg, founder of Johan Lundberg AB, sees many advantages in the new MTBM: “We have long been searching, asking and hoping for a solution for drilling in hard Scandinavian rock with active steering that can be used in projects where requirements for precision are high. For longer drillings this has previously not been possible unless the inner dimension exceeds 1.20m (manned entry). Larger dimensions are often required in Scandinavian rock for the machine to have the required strength, as well as for meeting requirements for work environment when replacing discs.
“We are happy and grateful for the excellent collaboration with Herrenknecht, and that they now have produced an equipment that meets our requirements. The project in Edsberg proves that this now can be done, and together we have moved the boundaries for what is possible. For this we are very proud. We believe that many will benefit from the opportunities springing from this progress.”
COMPLEX TUNNELLING PROCESS: NEW CHALLENGES IN EDSBERG
The new machine type completed its first practical tests in Germany back in 2017. The first applications under real conditions followed in 2019 in Australia (L=100+40m, UCS: ~185MPa) and 2020 in Hong Kong (L=107m, UCS: ~200MPa) with the jacking of concrete pipes. It was different in Edsberg: there, the tunnellers not only had to dispense with a target shaft. Due to the nature of the extremely hard and stable rock, no concrete pipe or other lining is planned for the tunnel there. The tunnel walls are formed directly by the rock. It was therefore necessary, for the first time, to drive a temporary steel pipe with the AVN 800 HR in order to be able to pull the MTBM back to the launch shaft.
To complete this challenging task, the tunnelling experts from contractor BAB Rörtryckning AB were able to rely on Herrenknecht on the jobsite too: “Herrenknecht was a very good partner not only during project preparation, but also during construction,” says Magnus Tingstrand from BAB Rörtryckning about the collaboration. “We had valuable support from our Herrenknecht colleagues on site at all times, enabling us to work together as a team to fully utilise the capacity of the AVN 800 HR, which is specially designed for hard rock, to achieve good tunnelling performance and to successfully implement the project with its special challenges.”
First, the main contractor PEAB Anläggning AB blasted an approximately 8.0m x 3.5m launch pit 7m deep into the rock. Then BAB Rörtryckning AB placed the AVN 800 HR on a jacking frame especially designed for the 6m long steel pipes. As in normal pipejacking, this successively presses the individual pipe segments forward behind the machine, which then form a continuous pipe string.
In order to keep the jacking forces as low as possible, the pipe string is lubricated with bentonite during jacking. A volume-controlled lubrication system enables a very precise and targeted introduction of the bentonite into the annular space, so that the tunnelling alignment is supplied with defined injection volumes to the exact metre. The targeted primary supply to the tunnelling machine ensures that the lubricating film does not break off.
Unlike other projects, Edsberg did not involve reinforced concrete jacking pipes, but rather steel pipes with an inner diameter of 1042mm and an outer diameter of 1067mm (nominal width 42”). And another thing that was new about the project: the jacking frame is not only pushing the MTBM and pipes forward, but also pulling for retraction out of the tunnel. The special steel pipes and the jacking frame have been well designed and manufactured by contractor BAB Rörtryckning AB.
In fact, the machine was only pulled back to the launch shaft twice during the drive: after the first 20m of tunnelling, BAB Rörtryckning AB and Herrenknecht carried out an inspection of the cutting tools in the shaft, but they showed virtually no wear. The one and only replacement of the TCI roller bits was then only necessary after 72m. After breakthrough, the machine with its cutting head was pulled back to the launch shaft as planned and the pipe string was gradually dismantled.
Finally, a stainless steel pipe with OD of 950mm was installed in the bored hard rock tunnel to connect two existing sewer tunnels, and the annulus space between stainless steel pipe and rock was injected with cement.
The Herrenknecht.Connected digital solution ensured that everyone involved was always informed about the tunnelling and machine data in real time. The manufacturer’s customer portal virtually maps the machine operators’ cockpit monitors. Web-based analysis tools thus provide users of Herrenknecht Group machines, deliverables and services with comprehensive insights into all key parameters, processes and events, anywhere in the world. The core function of these digital tools is to allow jobsite and project management to monitor all data relevant to tunnelling, regardless of location and time. This includes a wide range of automated analysis functions, clear dashboards and detailed sensor data evaluations.
In practice, this means the experts can make optimal use of the machine’s sophisticated control concept during ongoing operation. This is because parameters such as advance pressure can be optimised remotely at any time depending on the situation. This allows the machine’s capacity and performance to be fully utilised.
PROJECT WITH APPEAL FOR INDUSTRY
The go-ahead for tunnelling in Edsberg was given at the end of August 2023. Work progressed at a rate of up to 6m per day or 31.5m per week. After just two and a half months, on 9 November, the breakthrough into the Käppala Tunnel took place.
“To bring the trenchless methods further and break new records is very motivating and if you can do it and still have peace of mind while doing it, it is even better,” says Tingstrand.
The new machine concept of the AVN 800 HR has thus proven that the excavation of microtunnels is possible even in hard rock and in the non-accessible diameter range over a length of up to 200m, and with very high precision in the range of millimetres. At the same time, energy consumption, vibrations and noise emissions are reduced compared to alternative methods.
Use of the new AVN 800 HR is not limited to applications in hard rock. Depending on the prevailing conditions, it use can be extended to a larger diameter and also be equipped with a standard or mixed soil cutting wheel.
HUGE INCREASE IN PERFORMANCE
For the tunnelling industry, this means that in small-diameter hard rock tunnelling, the ongoing enhancement of technologies continues to make a significant contribution to extending the previous limits of drive lengths while constantly improving performance. As a result, the range of applications for microtunnelling has grown more and more in recent decades and increasingly sophisticated projects for underground utility systems have become possible.
But even in the face of new developments, ground conditions still play an important role. They determine the limits for routing and the possible use of trenchless construction methods. Particularly in hard rock with high rock strength and/or abrasiveness, the applicability of microtunnelling was limited in the past, especially in the area of non-accessible diameters. This has changed with the Herrenknecht’s new AVN 800 HR machine.
With the increased drive lengths now possible and the further development of trenchless technologies, microtunnelling is becoming an increasingly economical and environmentally friendly construction method. Not least, the number of shafts required is reduced. For certain projects, it is also possible to avoid the construction of larger tunnels used only for access. The impact on the surface is also considerably lower. This improves public acceptance. For clients, planners and consultants, this opens up completely new possibilities for the realisation of tunnel alignments for a wide range of infrastructure facilities.
CONCLUSION
In recent decades, the range of applications for slurry microtunnelling machine systems has expanded significantly: increasingly sophisticated projects for underground utility systems have been designed. Nevertheless, ground conditions continue to play a key role: they determine the limits for routing and the possible use of trenchless construction methods. In hard rock, the applicability of microtunnelling has been limited in the past. The AVN 800 HR now enables drive lengths of up to 200m without interventions, even in complex hard rock and in the non-accessible diameter range.