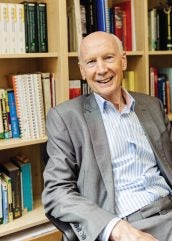
He is also Lord Mair CBE, FREng, FICE, FRS having been raised to the peerage in 2015, which means as a crossbench peer he is an independent voice for the profession in the House of Lords. He spoke to Julian Champkin
Engineering is in Robert Mair’s blood. So is Cambridge, where we met; so is being a Professor of Engineering at Cambridge. All of that is due to his father, who was also a Professor of Engineering at that same university.
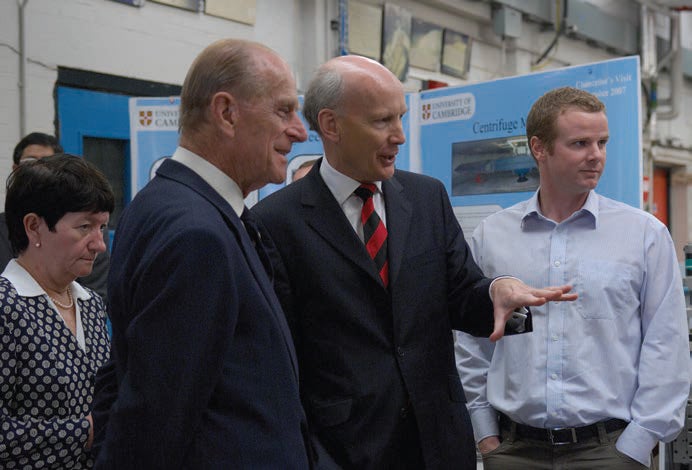
“It’s true that my father did have a pretty big influence on my life,” says Mair. “He was an aeronautical engineer. He built windtunnels at Manchester University, then at a very young age was appointed Professor at Cambridge: he was 35 at the time and I was two. So I grew up in Cambridge and was at school here. My father was very much an experimentalist and I think that has influenced me; but I did mentally resolve not to go anywhere near aeronautical engineering simply because that was his thing. So I went in the opposite direction, underground.
“But I also went to university here in Cambridge as an undergraduate. And I was very fortunate because that was a time when soil mechanics was really becoming a major subject, which it hadn’t really been before. One of the principal reasons was the Aberfan disaster. In 1966 a coal tip outside the village of Aberfan, which had been stable for a long time, just completely without warning liquified and flowed at about 30 miles an hour straight down the main High Street and engulfed the village school. 166 children were killed.
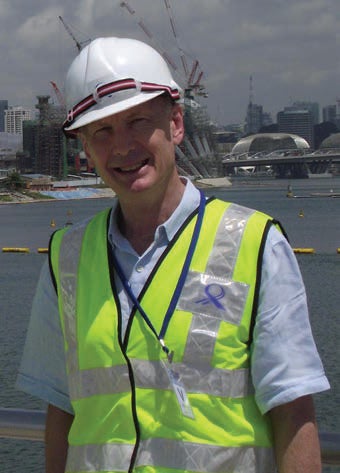
“Like almost all problems in geotechnical engineering, water was at the root of the problem: unbeknown to everyone the tip had been built on a spring and the water pressure built up inside until there was a shear failure and it liquefied.
“That of course raised awareness in a big way. The government immediately pumped a lot of money into research on soil mechanics, and Cambridge University was a beneficiary of that. So when I arrived as an undergraduate, all of the talk in civil engineering was around soil mechanics.
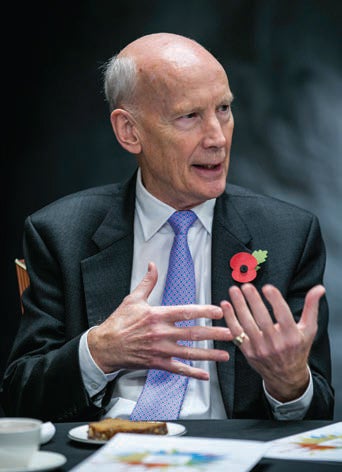
The project I did in my final year was on liquefaction, simulating it with special triaxial testing machines which were trying to recreate the kind of phenomenon that was seen at Aberfan.”
When he graduated he got a job with Scott Wilson Kirkpatrick. “What attracted me particularly was that they had their own soil mechanics laboratory, which was very unusual for a consultancy firm.
“Their head office was just off Oxford Street, in a building with six floors, and on one of the floors was a soil mechanics laboratory. Right in the middle of London. I thought that was terrific. Then, when I was 23, they sent me to Hong Kong and that really changed my life.
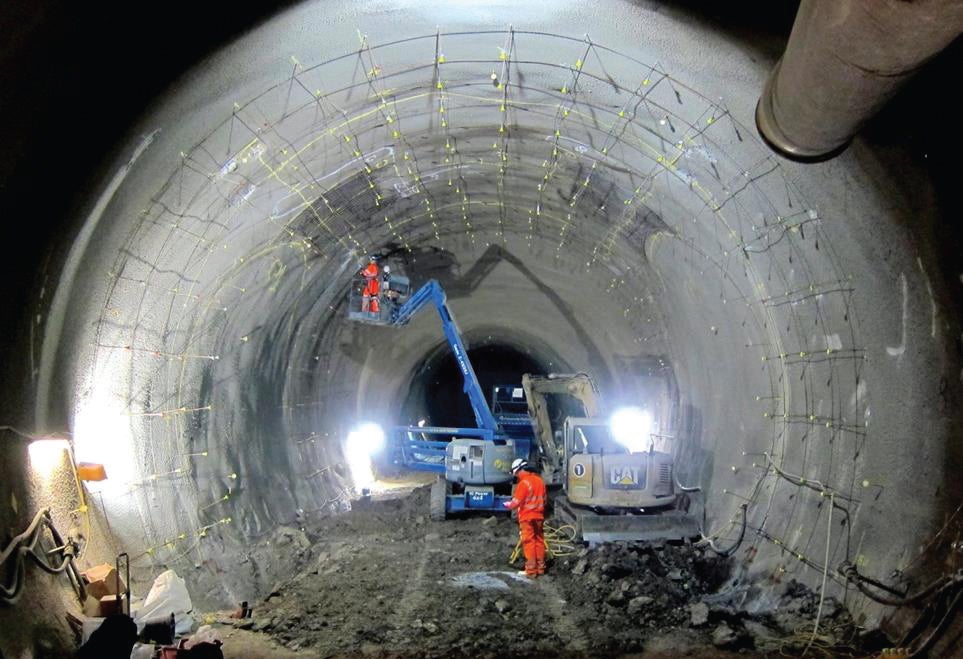
“When I went out there in 1973 the first tunnel between Hong Kong and Kowloon was just being finished. It was an immersed tube tunnel rather than a bored one. I was not actually working on it but it was very formative for me. It was the time when the Hong Kong government was seriously thinking about designing and constructing a new metro. Ground conditions were very complicated and there was a worry about the stability of buildings because Hong Kong was already very built up and at that time comparatively little was understood about predicting stability and ground movements when you’re constructing a tunnel in soft ground.
And I was lucky enough to be in the right place at the right time because back in the UK the Transport Research Laboratory, called then TRRL, the Transport and Road Research Laboratory, under the wonderful Myles O’Reilly, was directing a lot of very good research on tunnelling. Myles awarded a research contract to Cambridge University to investigate the very thing I’ve been talking about in Hong Kong, ground movement and tunnel stability in soft ground. Which meant that Cambridge were looking for somebody to do that research, and that fell to me. “So I came back to Cambridge aged 26; and it was a very exciting time because what Cambridge had was a brand new geotechnical centrifuge. It was the brainchild of Professor Andrew Schofield who was head of the soil mechanics group and it was the equivalent of a wind tunnel in aeronautics.
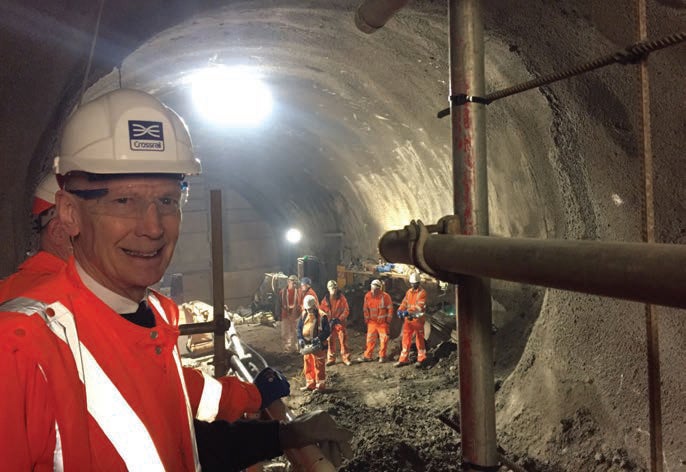
“If you want to study the behaviour of a plane you can scale it right down to a small model, but you have to blast air through the wind tunnel at much higher speed so that things like Reynolds numbers model properly. Similar scaling laws apply in geotechnical engineering. The driving force behind the instability of a tunnel is the weight of the ground above it, so if you construct a model tunnel at, say, 100th scale in a block of soil, you need to accelerate it to 100g to get the stresses that are equivalent to full scale.
“All of which meant that the centrifuge, which was 8m in diameter, had to spin at around 200rpm. It was a big beast. And I was very fortunate to be one of Andrew Schofield’s very first PhD students. We essentially spent three years constructing model tunnels in different sorts of clays and photographing them under controlled conditions while they were being accelerated at very high g forces until they collapsed. And, through image analysis, the photographs showed the deformations on the way to collapse.
“Like all these things, there were quite a lot of factors involved – the tunnel geometry, the geotechnical profile and properties, pore pressures and many more – but I think the art of good engineering is to distil down what are the major phenomena, and it turned out that there were relatively few. That meant we were able to generate some quite important new ideas about stability numbers and ground movements.
Those were the days when quite a lot of tunnels were still being constructed in open face conditions, and what these centrifuge tests really enabled was an assessment of how feasible it would be to construct tunnels in clays with or without face support and whether it would be safe to do so.”
After that, he went back to Scott Wilson for a few years and then then set up his own company. “We called it Geotechnical Consulting Group, GCG. I set it up with a lifelong friend and colleague, David Hight, and with Peter Vaughan, who was a professor at Imperial College.
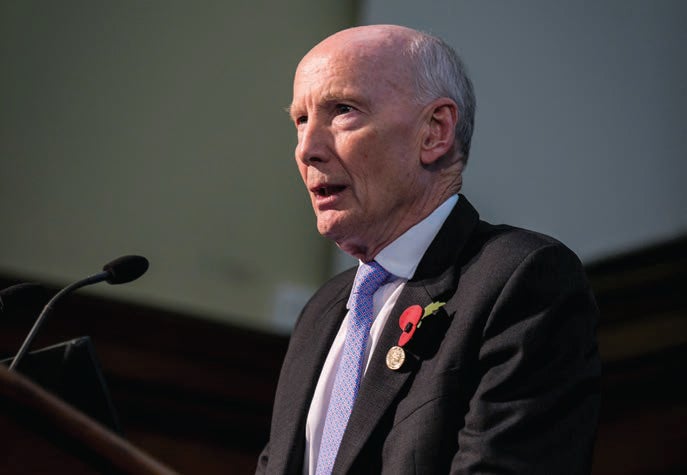
“Peter was an outstanding professor and he saw that there was a real need for highlevel consulting in geotechnical engineering, and that was what we saw GCG as doing: taking the very latest developments from soil mechanics research groups and applying them to practice.” GCG celebrated its 40th birthday last year.
“We worked on the Jubilee line Extension and on Crossrail, and anything to do with geotechnical engineering, but the tunnelling part of its work was my major interest. We did a lot of work with London Underground, and I got involved in projects in Turkey, Barcelona, Singapore, Hong Kong, and many other countries.
It was for London Underground that compensation grouting first came about.
“They needed an escalator tunnel, a large one, to go down to Waterloo underground station, but it had to pass extremely close to the foundations of the Victory Arch, which was built in the 1920s as a Great War memorial and it is the main, and iconic, entrance to Waterloo station.
“It is made of marble, it is extremely sensitive to movement. This escalator tunnel of 10m diameter was to go right underneath it, within 1m2m of its foundations; and, any cracks appearing in it would be very bad news indeed. The escalator was also going right underneath the Waterloo and City underground line – the ‘Drain’ as it is called, which was built in the 1880s – so that was fairly delicate, too. George Sabine, who was the chief engineer of London Underground, came to us and said ‘How can we do this?’ And that’s when we developed the concept of compensation grouting, a major refinement on previously existing grouting techniques, principally in respect of very accurate subsurface and surface ground movement measurements, using novel monitoring technologies, in conjunction with carefully designed grouts.
“Following grouting trials, where the ground was excavated to inspect the detailed effects of the grouting, we specified the installation of tubes in the ground between what would be the tunnel and the foundations above; and, during tunnelling, with extremely accurate monitoring of the subsurface and surface ground movements as well as the overlying structures, using innovative electrolevels and extensometers, you could then inject from those tubes very well defined amounts of carefully designed grout, in very small quantities, to precisely compensate for the movements that would take place because of the tunnel construction. And, if you can get that to work optimally, the foundations of the overlying structure barely know the tunnels are being constructed beneath them.
“Hence the word ‘compensation’ – with the term ‘compensation grouting’ coined by my GCG colleague, David Hight (Mair and Hight, 1994).
“George asked if it had ever been done before and I said, ‘No, not in this form. But I’m confident it will work.’ And what I think was terrific of George Sabine was he gave us the go-ahead. He had the vision to say ‘Okay, these young engineers have really thought it through. They’ve convinced me.’ I think it’s fair to say that that nowadays that might be more difficult for anyone in his position.
“There are all sorts of refinements needed in compensation grouting, such as the mix of grout, the viscosity, the injection pressures and so on; but the key to it, one of the driving principles, is accurate measurement.
If you know the whole time what is happening, where the ground movements are developing and their magnitude, with innovative technologies for subsurface and surface monitoring, then you know exactly what you need to do to compensate.
“So that escalator tunnel was built successfully without any damage to the overlying Victory Arch and the Waterloo and City Line tunnel. We had a lot of visitors, from consultants and from contractors, and the compensation grouting worked brilliantly because the maximum movement of the Victory Arch and Waterloo and City Line tunnel was only about 15mm. Without compensation grouting it would have been 100mm plus, which would have been extremely damaging (Harris et al, 1994; Mair et al, 1994).
“And this led to the technique being widely employed on the Jubilee Line Extension, and especially to protect Big Ben. This, for me, was probably the biggest thing I’ve been responsible for, and as I’ve said on many occasions it was the time when I lost any remaining hair I had. But it was a fabulous bit of engineering involving a lot of engineers, a lot of teamwork.
“They were constructing the new station at Westminster for the Jubilee Line Extension, and that station is one of the deepest in Europe. Just to put it in perspective, it goes down almost 40m below ground level and only 30m away is Big Ben on shallow foundations. So the tower was going to be very much influenced by the construction of the station and associated platform tunnels.
“The Victorian engineers who built Big Ben, back in 1843, are much admired and were sometimes brave but they didn’t follow modern building regs. When they were constructing it, quite close to the River Thames, they dug down until the water was pouring in so much that they had to stop, and then they poured in what we would call fairly basic mass concrete. That is the foundation of Big Ben. It was pretty primitive and because of the height of the tower it is under very high pressure. To complicate matters, it had been steadily moving ever since it was built. To the naked eye, the tower was still vertical, but there was clear evidence that it was tilting.
“So, you had an already leaning tower and this huge great station and platform tunnels were going to be constructed beneath it. Based on the success of the Waterloo Escalator tunnel, the decision was taken to protect the tower with compensation grouting.
“They put a shaft down in Bridge Street just before you cross the River Thames, then drilled horizontally in the London Clay many tubes for a distance of about 50m under the foundations of Big Ben. And that was all done in advance of the construction of the 40m deep station or the 10m-wide platform tunnels. Then, during construction over a period of about three years regular grout injections were done, and every single day Big Ben’s movements were accurately measured and reported, thereby enabling decisions of how much grout was to be injected, through which tube, and when.
“The beauty of the system is that these tubes have holes in them, about 600mm apart; and each hole is covered with a rubber sleeve, rather like a cricket bat handle. This prevents anything flowing into the holes, but when you want to inject, any one hole can be selected and the grout can flow out through it into the ground.” Big Ben’s tilt monitoring can best be expressed by the horizontal movement of the centre of the clock. The clock is 55m above ground level and the horizontal movement of the centre of the clock was set to not exceed 25mm during construction.
“For the first year, because the business of grout injection is something you don’t want to do unless you need to, no grouting was undertaken until the movement reached 15mm, at which point grouting started. For the next two years the movement was held between 15mm and 25mm (Harris et al, 1999).
“The process was very organised. Injections were pretty much stopped when the construction stopped. But those tubes are still there so if it was ever thought necessary, there could be further grouting.” After that, in 1998, Cambridge called again. “Andrew Schofield, my old professor, was retiring and they persuaded me to come back as Head of Civil Engineering.
“It took a lot of thought to return to Cambridge. I was 48 then. I think the final persuader was that the vice-chancellor at the time was Alec Broers. He had been Head of the Engineering Department; he’s an electronics engineer – in fact he very much pioneered the chip nanotechnology – and he felt very strongly that there’s a need for high-level university engineering departments like Cambridge to have very strong links with industry. He wanted me to bring all of the practical tunnelling geotechnics experience that I had.
Cambridge saw it as a big advantage, and I saw it as a big challenge because it could work both ways. It could be very valuable for the students and valuable as well for industry, if research programmes at Cambridge were addressing problems that are still unsolved and affecting tunnellers and geotechnical engineers.
“It has been a really interesting thing to see happen, this synergy between industry and academia.
“And I think it paid off. We have built up a very big group: the Geotechnics Group at Cambridge has become really quite large, with a lot of young people who want to do PhDs that they could see has real relevance to practical engineering. And I enjoy the contact with the students. It’s important for all academics to be challenged by bright students, and we certainly have a lot of those, from all over the world.
“And it’s actually very broadening, too, to sit down at lunch or dinner with a range of disciplines – scientists, geographers, classicists, historians, and many more. That is one of the great merits of the Oxbridge college system.
After his appointment at Cambridge, he retained his Senior Partner position with GCG and remained closely involved with industry, much of his work being on tunnels, including membership of the expert tunnelling panels for Crossrail and HS2. He also became President of the Institution of Civil Engineers (ICE) 2017-18, the year of the 200th anniversary of the ICE. “It was a huge privilege to have been the 153rd President, following the first President, Thomas Telford, 200 years later. During my Presidency, I was fortunate to visit many construction projects both in the UK and overseas. One that stood out was the Tuen Mun – Chek Lap Kok underwater road tunnel in Hong Kong, 50m below sea level.
“My more recent interest has centred on smart infrastructure and construction. One of my colleagues, Kenichi Soga, was a young lecturer in the Geotechnics Group when I arrived, and we had a real synergy because I was bringing all sorts of problems from industry that were yet to be solved and he had a lot of ideas for solving them. We worked very closely and just over 10 years ago we saw the digital revolution was coming. It has brought with it an absolute explosion of technologies to do with measurement. So we applied for and were awarded a major grant to set up a new centre called the Centre for Smart Infrastructure and Construction, CSIC. Its purpose is to exploit new sensing technologies for the benefit of all sorts of civil engineering applications, including tunnelling.
“What we are really talking about here is infrastructure. It is taking further forward the same ideas that were central to compensation grouting: if you are measuring everything really well, you can control things much better. You can do more ambitious things if you have an absolutely clear picture of what is happening.
“Lord Kelvin, back in 1883, famously said that ‘if you can’t measure it, you can’t improve it.’ I think that absolutely applies to our industry. By measuring we can make big improvements. And so that was the basis of CSIC.
“Our Engineering Department at Cambridge is unified: Mechanical Engineering, Civil Engineering, Electrical Engineering were all in one physical building and our undergraduate students in their first two years study all of them. So there’s terrific dialogue between the different disciplines, and that has played particularly well into CSIC.
“Kenichi and I were very taken by some of the new developments in fibre optics. We found that if you take a bog-standard fibre optic cable, the sort that the telecoms people put down every road, 98% of the signal is transmitted through the fibre and just a small percentage gets reflected back.
But if you have the right kind of device you can receive the light that is backscattered and you can interpret it in a way that tells you if the fibre optic cable is under strain, how great that strain is, and exactly where it is occurring. That gives you an amazing opportunity. One single cheap fibre optic is effectively a continuous strain gauge so you can put it into tunnel linings, piles, diaphragm walls, bridge decks, you name it.
And it is completely inert. It doesn’t require any electrics at all, it’s just a piece of glass. “And just as those tubes under Big Ben are still there to be used if needed, the fibre optic will be there in your tunnel 100 years from now and you will be able to use them to tell if the lining is in danger of cracking.
“This became a really very exciting development within CSIC. We were able to introduce it on Crossrail. Probably one of the best examples was in some of the sprayed concrete platform tunnels for Liverpool Street Station.
“Typically for such tunnels people worry about what extra lining thickness you need where you cut through them to make the connecting passageways. Here there was a first pass of sprayed concrete, and quite a lot more thickness was going to be applied, but after the first pass we installed fibre optics right around where the openings were going to be. And then we were able to monitor, with great accuracy, for the first time ever, the stresses and strains that were actually generated by knocking the holes through the lining for these cross passages. And we were able to show – which was really an excellent result – that the additional stresses induced by cutting the cross passages were much less in extent than had been predicted.
“In glass optical fibre you have a material that is cheap; it can go round corners and the light will follow it; and it gives you an accurate and complete picture of the strain, at any point in the lining, throughout the life of the tunnel. It had been used in other countries, but I think that was its first use in sprayed concrete. I think this will become standard fairly quickly.
“And so will other data measurement systems. One of the things that I’ve been constantly talking about ever since CSIC was founded is that tunnelling and construction is a naturally conservative industry, and we are in some ways our own worst enemies because of that. The aerospace industry and automotive industry are constantly innovating, and one of the underlying factors behind that is they measure. They measure everything. There isn’t an aeroplane that takes off now which isn’t riddled with sensing devices. They know everything about how its behaving, including its engines, in the air, on the ground, all the time, and in real time.
“In comparison, we in the construction industry might complete a beautiful bridge, and you might say to the structural engineer, ‘It’s a wonderful accomplishment. How is it performing?’ and more often than not the most they can say is ‘Well, cars are driving across it…’”
“This reluctance to measure could be psychological. I remember quite a long time ago we were proposing to do some detailed measurements of strains in a diaphragm wall. The senior partner of the firm responsible for its design was rather reluctant to know what the actual measurements were.
“I think it was because he didn’t want to be exposed for making probably very conservative decisions about their design. And this goes to the core of what I really believe in. We have been using the same codes of practice, the same design methods, for decades, and that is fair enough when there is uncertainty. You, of course, have to err on the side of safety.
That is paramount. But if you are measuring, and showing the strains and stresses to be less than expected, instead of estimating them, you can afford to be less conservative because you know that there is room for substantial optimisation. It is simply health monitoring for infrastructure. Consider the dramatic example of the Morandi Bridge that collapsed in Genoa. It didn’t have a single sensor on it. Had it done so, it would almost certainly have been closed to traffic long before it collapsed, and lives would have been saved.
“Not so long ago, CSIC was approached by Network Rail about the railway viaduct at Leeds Station. It is a classic Victorian viaduct, and there was spalling and there were cracks in the brickwork. Network Rail were so worried that they had imposed speed restrictions and were even contemplating replacing the whole thing, at immense cost and disruption. We installed some fibre optic sensors which showed that actually the viaduct was performing perfectly well and the cracks were not affecting the inherent performance of the structure. So they lifted the speed restrictions and abandoned any thoughts of replacing it.
“I think our industry is coming round, but it remains curiously reluctant to spend very small sums on routinely installing sensors in capital projects. I talk to aeronautical engineers, automotive engineers, and they are astonished that civil engineers don’t do this much more routinely.
“We are now in the digital era of Big Data. It’s not a question of it’s coming, we are in it now. I opened the session on ‘Frontier Technologies’ at the WTC 2023 conference, in Athens, and we talked about artificial intelligence, AI. I think that the underground construction industry is ready-made for a lot of very interesting developments like that.
“One of the big uncertainties in tunnelling is the ground. No matter how many boreholes you drill you never quite know what is there; you never have the ground conditions completely nailed, so to speak. You know that it’s variable; and with even the most versatile TBM you can run into unexpected difficulty. This would absolutely be a place to apply AI.
“A TBM can send signals into the ground ahead and get signals back, which at the moment may appear unintelligible.
You see some of the outputs and you think ‘how do I make any sense of that?’ But AI could interpret them by combining such data with other measurements made by the TBM and with high quality borehole measurements. There’s a big future, I think, in improving our knowledge of the ground and predicting its behaviour as a TBM advances. There are frontier technologies that really are changing the way we can do tunnelling; and they are with us now.