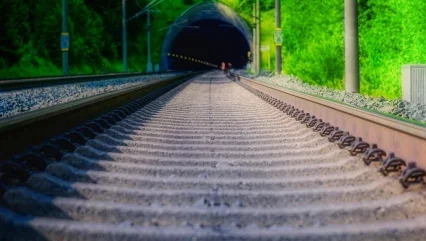
Ross Dimmock has worked on major tunnelling projects from early in his career and is well known in the UK and internationally. From the early years with contractor Transmanche Link (TML – coming from Tarmac) on the Channel Tunnel, he moved onward to eventually work on A3 Hindhead road tunnel, in Surrey, and Crossrail in London.
Over the years, he has had varying roles that crossed traditional career boundaries and, in so doing, broadened his experience and expertise. Dimmock has worked successfully in consultancy (Mott MacDonald) and contracting (Balfour Beatty), and research (Transport Research Laboratory – TRL) and also materials specialists (BASF). He is now vice president for tunnelling with Normet.
Pulling upon 34 years of sprayed concrete lining (SCL) experience in tunnelling, Dimmock told the meeting that a key challenge in his role is to lead the development strategy for sustainable, low carbon solutions, a passionate focus of his. He is motivated to see change come about and it was natural, therefore, that the theme would be the focus of his BTS lecture – ‘Small Steps Forward in Sustainable Sprayed Concrete Tunnels’ – given in January and held online due to the then ongoing restrictions borne of the covid pandemic.
SUSTAINABILITY SPREADS
First off, in beginning the lecture, he observed that low carbon with SCL and concrete to support sustainability is still a developing area of knowledge – “it’s not written in stone that it is a new topic, I think there are still a lot of questions.”
The presentation covered his views on developments with SCL, in particular taking in the bigger picture of international objectives and policies regarding climate change and practical ways for low carbon approaches to be undertaken in tunnelling.
A few areas of focus were highlighted: how he has been influenced about sustainability; how SCL has developed in the UK in ways that “sets us on a good footing” for a low carbon future; some SCL project experiences about sustainability, much of it from Norway; and, ways to leverage the knowledge and experience more widely.
Dimmock noted that one of the side-effects of the pandemic shutdowns, for all their difficulties, was less traffic and pollution and a fresh appreciation of nature and environmental possibilities.
A further point hightlighted was the visibly successful emergence, albeit through necessity, of more collaborative behaviour in areas like medicine to achieve a massive goal in providing health protection to our global populations. But there were also changes in how others could, and did, come to together to connect and work in new ways, especially if having to stay remote, not be on site much unless in a tunnel.
“I think a caring side sort of emerged.”
That also gave courage and more impetus, when reflecting upon the experience of the cleaner environment, to be “really looking at sustainable topics.”
The aspect of sustainability that Dimmock focused upon for the lecture was carbon emissions, or relative carbon quantities – an asset’s carbon ‘footprint’, in other words.
Looking at sustainability, and doing so through the lens of quantifying the relative amounts of carbon, Dimmock explained he had interesting discussions and helpful insights from key people who influenced his thinking and exploration of the themes, including:
- Rachel Skinner, Past President of the Institution of Civil Engineers (ICE), who brought a message that as part of ‘net zero’ pursuits’ there is a need to consider climate change adaption needs and to support looking after ageing infrastructure, an idea that is coming more to the fore;
- Lewis Barlow, who leads the Carbon Team at Sweco, advising UK government teams on low carbon infrastructure development, and in his spare time is an ICE tutor on carbon management, instruction in which “really opens up your mind” to its practical implementation on projects;
- the all-things-SCL expertise of Tom Melbye who grew Normet and will present on the topic at the next World Tunnel Congress (WTC 2022, Copenhagen);
- Dr Keith Bowers, a director of consultancy COWI, whom Dimmock has known since their TRL days, and who gave the Harding Memorial Lecture 2020 on ‘Tunnelling in a Changing World’, covering many aspects of sustainability and carbon in the industry as well as digital, modelling and multi-use possibilities for underground assets, and more; and,
- Dr Alun Thomas, of All2plan Consulting, who has “started to put numbers and breakdown where carbon is” which has been very useful, helping to focus on things needing done “to get it right.”
DECADES OF EVOLUTION
Much progress with SCL in tunnels has been made in recent years, Dimmock observed, providing a quick overview of its development over the last few decades in the UK, starting with early use of shotcrete to create a large span cross-over cavern under the seabed for the Channel Tunnel.
Of that project, he recalls dry-mix hand spraying operated at up to 3m3/hr, almost a third rebound, alkali-rich accelerator was shovelled in at the pump and burnt the skin, spraying hoses burst, and strength achieved was often not much more than 18MPa at 28 days. Lattice girders and steel mesh were installed without face sealing shotcrete.
Construction conditions were extremely challenging and then technical performance of the material then is marked contrast to what tunnellers can expect to be achieved today – the same level of strength gain in less than half a day and with far superior, and safer, working conditions and materials. The improvements were won as technology was developed and proved, and improved, over numerous subsequent projects.
With brief references to the many milestone tunnel projects that followed in the UK, in the 1990s, such as on Jubilee Line Extension, Heathrow Express and the Channel Tunnel Rail Link, Dimmock noted that wet mix SCL had less dust and rebound. However, he recalled high face inspections still being facilitated inside baskets strapped to the front of roadheaders – not something for current practice, at all. Then, the primary SCL lining was taken as temporary lining, for design purposes, and the secondary continued to be required, applied by nozzle operators.
The first permanent sprayed concrete secondary linings arrived, especially after the Heathrow tunnel collapse in 1996.
Then, as more developments arrived, robotic spraying came along – “the robots came quite quickly.” Operatives were left to hold switches rather than heavy nozzles, in the end, on the A3 Hindhead tunnel where permanent primary lining had arrived, along with spray waterproof membrane, plus cast in-situ side walls and the roof was SCL. Many technologies were establishing themselves, including sharper, remote profile control as well as the spray membranes – “and that was quite some time ago.”
In Dimmock’s experience of both the equipment and design side of the industry, he saw “how we really removed” mesh and girders as support. Execution of smoothly accurate SCL profiles were much improved. He acknowledges that progress “obviously driven by previous work from Morgan’s and Colin Eddie and others,” all creating a safe environment that no longer put people close to the shotcreting environments at the face – “a really great change and still not all that well adopted globally.”
In London, the more recent tunnel projects of Crossrail and the Northern Line Extension both benefited from all the points of progress achieved to enable permanent SCL (PSCL) linings to be constructed – permanent primary and secondary layers with, in between, a thin regulating layer plus a sprayed waterproof membrane.
“Things have really changed,” Dimmock told the meeting.
Further projects benefiting from modern SCL include the Thames Tideway super sewer, in London.
The ability to deliver smooth SCL profiles also brings into focus the methods of survey and profile control, in conjunction with the behaviour of the ground. Where the profile is consequently more of a challenge to smoothly achieve, the variability in dimensions often causes over-excavation to ensure that the minimum thickness of SCL in the design is achieved.
When building up the SCL layers there can be excess use of shotcrete, therefore, perhaps by 50%-100% more than is anticipated at the design stage, Dimmock estimated.
While geology leads to variation in excavated profile against plan, the use of PSCL, and moving away from multiple layers in SCL, should help to achieve layers that are less thick – for each layer has its own spatial tolerances, needed to ensure they are achieved, and also for requirement of ensuring safety and minimising risk. The effect is cumulative. They all add up to more excavation and more concrete being used which is not supporting our sustainable targets.
But need not do so, quite so much.
In one study, Normet, with consultancy BEDI, looked back in this regard at the original SCL layer design for Crossrail. The findings of their study suggest that, if done today, a thinner lining could be possible for the tunnel works which would also mean a reduction in the carbon footprint.
“I think it’s time to really look at full-scale trials with new technologies again,” Dimmock said.
In the meantime, there are benefits being gained from the development of photogrammetric scans of SCL tunnel works while construction is underway. Data on layers thicknesses is fed into 3D BIM models for comparison against plans. Real-time feedback from new 3D scanning tools enables adjustments to SCL placement while underway.
A further, spinoff benefit of closer monitoring of carbon would be more data on the use of materials, which would also contribute to discussion of potential areas of possible cost savings.
An additional thought, and which even contractors might come more to enjoy, is the potential for the thinner SCL lining to help create more architectural variety and curves in underground station and other, intricate, tunnel designs – even more than the corner curves in Crossrail stations. International interest is growing in what is being achieved in the UK.
MIX DESIGN CHANGES
While much improvement in SCL has been achieved over the last almost 40 years, Dimmock said one box has yet to be ticked – decarbonisation.
Systems today offer possibilities to potentially achieve 35%-40% of reduction in carbon load from the concrete used, which would correlate well with estimates by Dr Alun Thomas, in 2019, on what might be feasible to do in SCL tunnelling. The reduction possibility emerges from the many aspects of SCL – materials, design and equipment.. Each contributes savings in carbon.
“So, we can do quite a lot,” Dimmock told the meeting. “We can make big steps.”
On equipment for SCL, he anticipates that benefits can be gained from a number of factors, including training, battery electric drive sprayers and concrete transport, more use of automation in tunnel layer profiling, and use of computing technology for scanning, digitalisation technologies and rapid data analyses.
On materials, he recently calculated that a CEM I (standard Portland Cement) concrete mix design would have approximately 560kg of carbon per cubic metre. But where it is blended with other cementitious products, to be classed as CEM II – III, for example, the carbon footprint can be much less.
As example, Dimmock said a design possibility for a non-tunnel project showed that a blend of CEM I with ground granulated blast furnace slag (GGBS), on a 75:25 split, and with use of polymer fibres, could reduce the carbon load of the re-designed concrete mix by 40%- 50%.
The challenge for low carbon cements, however, is the slower strength gain early on even though their long-term performance is favourable. Early strength gain is vital for safety and building up thick enough layers during the SCL operations. Interesting studies with geopolymers have shown that mix designs could help obtain ultra-low carbon concrete with rapid early strength gain, although it then tails off after a week at lower than typically desired strengths (only almost 15MPa). Options exist to improve the strength.
NORWEGIAN ADVANCES
In recognising the strong position that the UK holds and the expertise with which the industry is viewed, in both SCL tunnel design and construction, and even while looking ahead to the challenges of decarbonisation, the experience here draws interest from overseas.
Such as from Norway.
The Norwegian method of tunnelling is typically to go lean, with limited thin rock support, perhaps including rock bolts. But sprayed shotcrete canopies are placed in road tunnels, using the protruding bolts to double-up as support props for linings and layers of insulation. In the gap beside the protruding bolt head, insulating PE foam is placed to stop drips of groundwater that could freeze and create hazards below. Sometimes the side walls of tunnels have precast panels put in place while only the roof is sprayed. Sometimes the full profile gets precast panels up and over, providing a high-specification visual finish, such as in road tunnels in Oslo and Bergen.
Both the rail and roads authorities are looking across to UK to examine what might be of interest to possibly use. The rail authority is particularly interested in the SCL advances, including thinner lining. But the roads authority, in seeking alternative to the fire risk of PE foam, and in already having inspection difficulties for the insulation behind, is also studying whether to go instead for sandwiched, multiple thicker layers with waterproof linings, which is a heavier design. The two paths have markedly different carbon footprints.
EARLY ENGAGEMENT WINS
Dimmock told the meeting that, as always with any project, it is early on that the key differences are made for outcomes and that development of underground infrastructure is no exception to this rule. He said that for tunnels it is at the design stage of project development where big savings on carbon performance can be found.
The carbon performance benefits would be best secured through client leadership. In that, the need for more budget spending would be a consequence of clients wanting better outcomes in low carbon performance. Part of this would then help to develop a more incentivised main contractor engagement during the planning and procurement stages.
Client leadership, therefore, is key to helping to engage the whole supply chain. Then, there would be alignment of all involved to help ensure each in the chain works in the best way through their re-envisioned relationships, and technical performances, to deliver more together in improved carbon outcomes in the developed tunnel project. This would be necessary for not only the construction phase but the entire life of the underground asset over the long term.
“Trying to make carbon savings during construction is really about just driving efficiencies,” Dimmock said. More can be achieved, he added.
Dimmock explained that the biggest carbon reduction gains for tunnel projects would come from decisions made earlier in the development process, primarily at the planning and design stages. He added that Publicly Available Standard (PAS) 2080: 2016 Carbon Management in Infrastructure would provide guidance on the upfront choices available for possible projects.
As part of that fuller assessment, the bigger view would be open to examining whether a new tunnel is always the answer; it might be that economic and environment assessments of how to approach a specific option in infrastructure investment might, instead, look at the upgrade or life extension of existing tunnels instead. New build should not be the default assumption.
While projects will be undertaken in future to develop new underground space, existing tunnels will have needs – and perhaps additional ones, he observed, in the era of potential effects from climate change impacts. The extensive flooding in Europe and Asia in 2021 affected many underground infrastructure assets, which need to be better protected, Dimmock stressed.
“It is one of those topics that we need to think about going forward.”
QUESTIONS AND ANSWERS
Following the lecture, Ross Dimmock took questions from attendees to the live online event, facilitated by the BTS chair. Below is a report on the Q&A session, selected and edited, and abbreviated, for clarity and space.
Q: How do you control shotcrete thickness without a physical profile?
Ross Dimmock (RD): To date, we use an interesting communication approach between a surveyor (or an engineer) and the nozzle operator (or excavator driver). The surveyor is on the side of the tunnel with a total station to put the laser around the profile and inform the operator or driver on adjustments they need to make. While being an effective method, it relies heavily on communication skills and technical skills of using the total station. From a spraying technology point of view, automation using 3D cloud scanning to give real-time feedback to operator is a strong, interesting possibility.
Q: How do you deal with wet rock surfaces?
RD: Challenges only begin to arise from significant water ingress. Damp and wet rock surfaces typically present no issues. Predicting the water ingress into the tunnels is therefore vitally important, helping to decide on the approach to use. Norway uses pre-grouting with micro-cement as a matter of course in rock tunnels. In London Clay, which is quite impermeable, we only see some seepage after a few months. In London, challenges can come from chalk and designers have a toolbox of ground conditioning measures, such as dewatering, but grouting ahead of the face can help with more serious conditions. Moderate water ingress can normally be channelled during spraying or by using dewatering holes ahead of the face. For lesser flow rates, strip drains and using slightly higher performing accelerators are usually sufficient. It is very hard to stop big rushes of water with spray concrete, you just need to try to control it before spraying.
Q: Why is there a division between technologies used by railways and highways for tunnel lining?
RD: I think the railways do not mind the finish of the tunnel. I remember learning with Keith Bowers and the Transport Research Laboratory (TRL) about the value of surface finish for road tunnels. The surface finish has to be optimum to provide high reflectance and ease of cleaning. This does not really bode well for sprayed concrete linings in road tunnels, you might think. However, at A3 Hindhead road tunnel and in Norway we have sprayed concrete linings on the tunnel roofs. Reflectance in dark rail tunnels is not required, so finish is not so important.
Q: Design optimisation can result in lower SCL thicknesses. Is it critical in comparison with material technology in achieving decarbonisation?
RD: Both would be ideal. If you can just do one, whichever it is, would be a change in a positive direction. We can decarbonise by changing our materials, by thinning the linings – but imagine if we did both. It would be nice to do everything in one big step, but that is unlikely. I call my presentation ‘Little Steps’ because we just need to take them – maybe material changes first, then design optimisation later, but both are possible and worthwhile.
Q: How can the thin lining approach demonstrate both its application and safety to reduce any reluctance in adoption?
RD: Development of solutions comes from the lab and then through scale-up tests to full-scale trials. For proving a concept, though, nothing beats building the real thing.
Q: Should clients start specifying requirements of green technologies to promote fair and competitive pricing among tenderers?
RD: Yes. I suppose it could be done in two ways, either with a performance criteria approach, such as based on the amount of carbon per unit length of a tunnel, or by getting more specific about types of technologies. To drive innovation, I would go with the former option, a performance criteria approach. But I do think we need to start pricing carbon and evaluating carbon in some way as part of the procurement process in project development.
Q: What are the key aspects to specifying a low-carbon shotcrete, without compromising safety and durability?
RD: That is the challenge we are faced with in the industry right now. We need to ensure that there is homogeneous mixing. We also need to ensure that there are minimum requirements stated by the designer in terms of material performance – I think this would allow some creativity in how we achieve it. There needs to be understanding of the durability concerns about some very, very low-carbon approaches in both concrete and sprayed concrete. With ground granulated blast furnace slag (GGBS) as a partial CEM I cement replacement – for which we do need to question how sustainable it will be in the long run – we do have a way of specifying how low carbon a concrete actually can be, using environmental exposure classes. Perhaps it could, instead, be done using carbon contents, which would give freedom to be more creative.
Q: What accelerators does Normet have available for ultra-low-carbon concretes?
RD: None yet but watch this space.