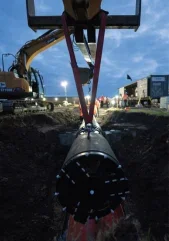
In 2020, a number of engineering and business students at ETH Zurich, in Switzerland, together identified an opportunity to contribute to valuable progress in a worldwide relevant area: tunnelling. Implementing this by working on a tangible product remained an undisputable goal from the beginning. It was decided to achieve this product goal by the students forming a team to self-develop their own tunnel boring machine (TBM).

This article highlights the project’s journey, its milestones, and technological futures of ‘Groundhog Beta’ – the TBM already showing promising results to challenge the status quo of conventional tunnelling.
Prior to this landmark decision to pursue the goal of achieving a breakthrough in tunnelling technology, some of the students had been involved in research for Hyperloop technology via the Swissloop team. This technology, of course, could make future highspeed travelling possible to an extent that is currently inconceivable. However, the students also became aware of tunnelling as a further opportunity to drive meaningful innovation that, in the end, could benefit the expansion of infrastructure systems on a global scale.
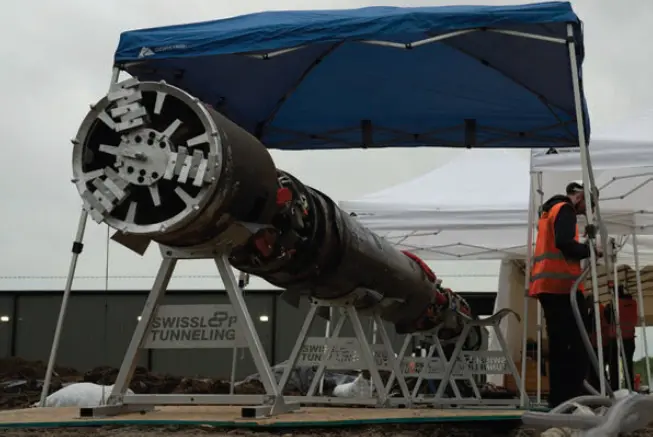
A new student-led team – Swissloop Tunneling – was formed that was more focused on the underground challenge. Upon its founding, Swissloop Tunneling started to identify the needs of the industry and society for both to be able to really capitalise on new tunnelling mechanisms in the future. Thus, with a long-term vision for the product, the team commenced their research and development aims with a design-thinking approach.
INSPIRATION
The Swissloop Tunneling founders got inspired by the futuristic concept of Hyperloop that would require hundreds of kilometres of tunnels. Therefore, they realised that it would always need to be considered how to develop a TBM that is highly scalable in terms of use. This should help in contributing to new approaches that could highly benefit society in the long-term future of mobility.
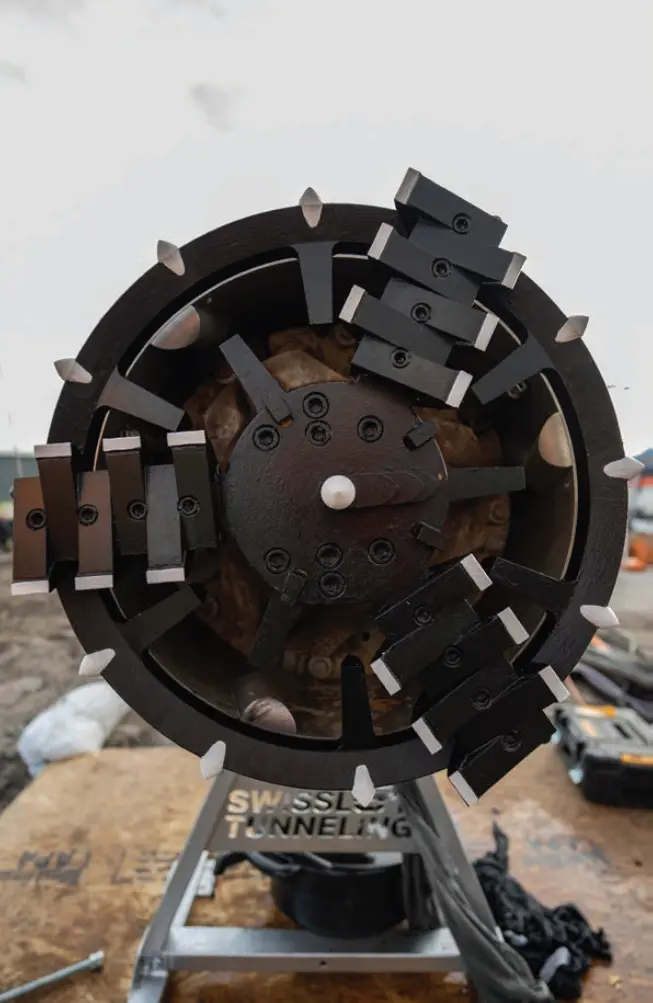
At the same time, Elon Musk initiated the ‘Not-a- Boring Competition’ with his company, The Boring Company, a startup which has set itself the goal to create scalable tunnelling solutions for innovative underground transportation systems. This competition framework would enable selected student teams from all over the world to come up with self-developed tunnel boring solutions and compete in different areas, such as innovation, guidance, safety, speed of machine launch, and, most importantly – building tunnels by boring faster than a snail can slither.
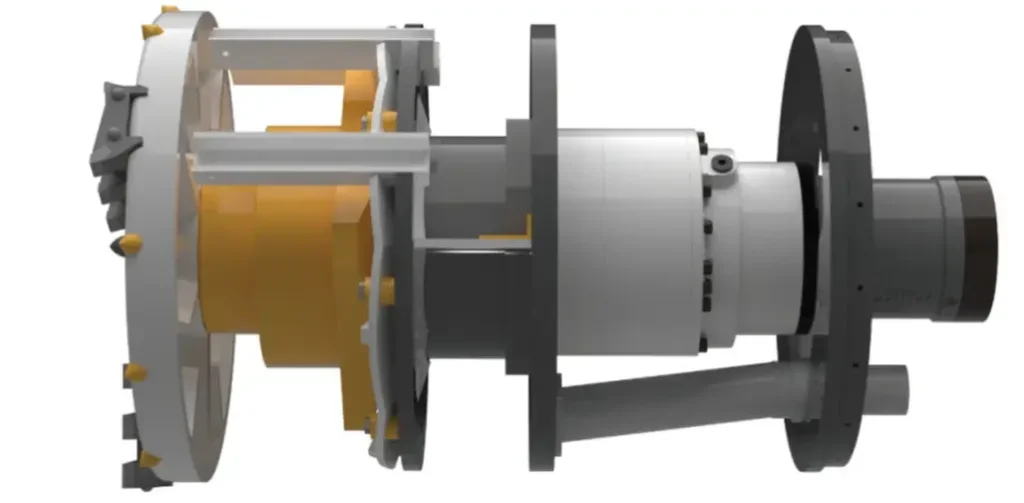
Thus, our then newly founded association, named Swissloop Tunneling, on the one hand knew there are evolving aspirations within the construction industry with the goal to make tunnel construction much faster and more efficient, in general. On the other hand, the Swiss association knew they wanted to take part in the first competition, which was scheduled for 2021, in Las Vegas. The event would enable the team to get in exchanges with other innovation-driven students as well as engineers with long experience from other countries with the same aspirations.
However, the first members of Swissloop Tunneling already knew that they also want to work on a machine that could significantly have positive impact for current construction that is taking place in the underground. Thus, they combined their aspirations for creating an innovative tunneling solution that is beneficial for present infrastructure requirements as well as futuristic concepts such as Hyperloop.
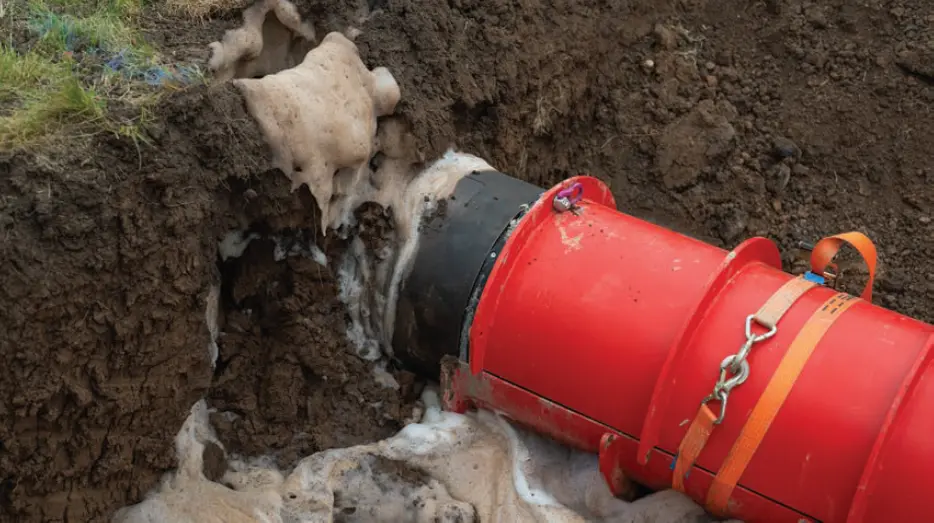
Nonetheless, both timeframes require very similar improvements of TBMs to unleash the potential of more efficient tunnelling projects.
Swissloop Tunneling decided to focus on the following: creating a TBM that moves faster and without interruptions, can autonomously dig a tunnel while only being externally controlled, and, in general, is more efficient in terms of financial, material and time resources.

Of course, the team of Swiss engineering students was fully aware of the fact that the tunnelling industry already aspires for more efficient machines. The founders’ desire was to contribute to this progress by getting into mutual exchange with various participants of the industry and they wanted to implement new approaches by working as a team – even though it could create moments of great difficulty for the young team of engineering students.

BEGINNINGS
After setting its goals, considering what the team sought to achieve with its TBM, and the successful application to take part in the ‘Not-a-Boring Competition’ of 2021, Swissloop Tunneling started to work on its prototype. At the beginning in 2020, the team also knew that it would need more talented people to work within the corresponding R&D framework. In addition, it was crucial to establish partnerships to get the resources and financial means to self-develop such a machine.
The founders brought together a team of many ambitious engineering students from across ETH Zurich and the project directly involved students from various disciplines, including engineering (mechanical, electrical, civil, materials, computer science) and geology, and business administration students have responsibility to manage the partnerships and public communications.
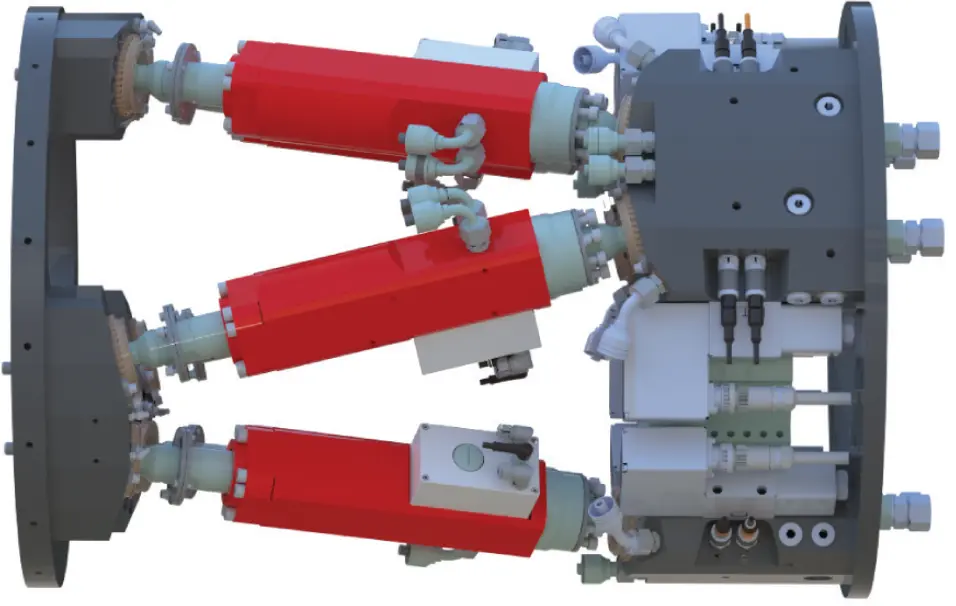
Finally, an interdisciplinary team of students with the highly valuable support of industry representatives and institutions was ready. The team has since grown. More than 100 passionate student members of the university have already participated at Swissloop Tunneling over these first years.
ENGINEERING: ‘ALPHA’ TO ‘BETA’
Within a year of its founding, in 2020, Swissloop Tunneling had invented, developed, and tested its first micro TBM (MTBM), named ‘Groundhog Alpha’. The MTBM was taken to the first ‘Not-a-Boring Competition’, in 2021, in Nevada. At the competition the MTBM and team did well; they won the award for Innovation and were placed 2nd in the overall competition. This participation was a first notable success along the project’s journey.
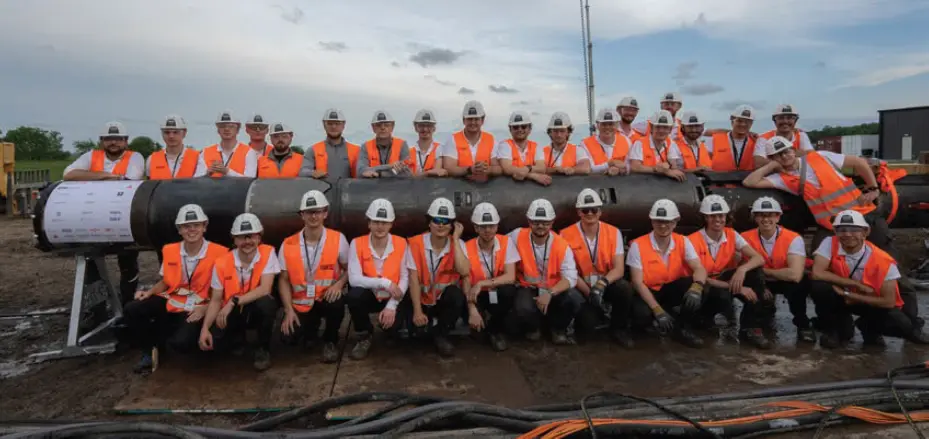
While maintaining the strong approaches of the Alpha model, the Swissloop Tunneling team decided to implement new subsystems and renamed the updated machine to be ‘Groundhog Beta’. With these new systems, the MTBM successfully participated in the 2nd edition of the ‘Not-a-Boring Competition’, held in Bastrop, Texas, in 2023. At this competition, the team once again was rewarded for the innovative approach of the new systems that became part of ‘Groundhog Beta’ but sometimes significantly differed from the Alpha version. Once again the team achieved 2nd place in the overall competition but also receiving the Innovation award.
The success of the adapted machine proved that the concepts within ‘Groundhog Beta’ are meaningful in terms of challenging the status-quo of tunneling technology. On the other hand, it became clear that it is now time to improve the reliability and to optimise the MTBM and support. This is why the team then invested all their efforts into optimising what they had learned from participating in the competitions – not only in technological terms but also with regard to the organisational arrangements within the team.
In the end, these invested efforts also turned out to be very successful. In the latest ‘Not-a-Boring Competition’, held recently in Bastrop, at the end of March 2024, Swissloop Tunneling achieved great success by winning the overall competition; after reaching 2nd place in prior competitions, the team and the technology gained the ‘Champion Award’ for 2024. This recent success is also proof that ‘Groundhog Beta’ has essentially progressed towards the vision of being used in the real world.
ENGINEERING: ‘GROUNDHOG BETA’
The technical features of Swissloop Tunneling’s current MTBM, ‘Groundhog Beta’, consists of the following:
Erosion: As opposed to the ground conditions in Las Vegas, where the team has faced a desert-like soil with the first MTBM, ‘Groundhog Alpha’, the ‘Groundhog Beta’ machine had its Erosion System adapted for the more cohesive, sticky clay conditions in Bastrop. As the Erosion System of the machine must process the underground material while digging, its actions take place at the front, within, and outside of the machine. At the front, a cutterhead with a crushing mechanism as well as a mixing element behind is placed, so that also mediumsized rocks can be divided into smaller ones. Since most of the soil in Bastrop consists of clay, the Erosion System also prepares the ground ahead of the cutterhead by conditioning it with a special foam mixture, which frees the processed soil from its cohesive consistency. As soon as the material is decomposed, it then gets transported through and out of the machine by using a suctioning mechanism. Outside of the machine, an external sedimentation system ensures the constant circulation of the involved water – enabling a recycling process by separating the reusable water from the eroded material.
Steering: This component enables the machine to dig at angles, in different directions, and to handle vibrations resulting from the machine itself. This part involves a lot of sensors to enable autonomous machine movement.
Lining: The next subsystem is in the middle part of the machine and is the Liner System. It represents one of the most innovative parts the project to achieve efficient tunnelling. The Liner system prints the tunnel wall while moving forward without interruptions. A pneumatic system transports polypropylene (PP) granulate into the Liner System. The PP granulate gets melted by heating elements, and the melted polymer is extruded, flowing to the outside of the machine where it cools to form the lining. Thus, the intended structure with strength to withhold the machine’s forces and pressure under the surface are achieved on the round surface of the machine. The result is a 15mm-thick tunnel wall liner that continuously gets extended as the ‘Groundhog Beta’ MTBM advances through the soil. Further, the tunnel wall could also be removed later, so that its material can be reused for the same or other purposes.
Propulsion: This part of the machine’s systems is crucial to getting the machine moving forward. The system involves the use of gripper plates, on the surface of the machine, which push against the surrounding ground; they are pulled backwards and then rearranged in continuous repetition of the process to deliver forward movement.
Support systems: To initiate the boring process, a starting platform is placed on the surface or in an excavated pit – dependent on what the user needs. The platform into which the machine is inserted can be adjusted for the desired angle to start tunneling into various directions. Also placed outside but connected with the machine in the underground, her sensors, and actuators – the software continuously monitors, analyzes, and controls the machine’s actions as well as status from the surface.
DRIVING AHEAD
The subsystems’ capabilities, the fact that they already have worked individually and as an integrative overall system, and winning the innovation-driven international competition, now gives Swissloop Tunneling confidence that it is on the right track and can fruitfully pursue technological development.
The team is planning the next steps to achieve the longer-term vision. Thus, the project now needs to identify where further optimisation is necessary and then implement what is required for further improvement. There must also be assessment of how the machine might even be adapted or extended to some degree for use in real-world infrastructure projects. These will require further intensive efforts in making more technological progress, and so, it is for sure that, Swissloop Tunneling will maintain the discussions and mutual exchanges as well as collaborations with the industry and institutions, to better understand the needs of potential users in the future.
In fact, the innovative approaches that are getting realised with ‘Groundhog Beta’ offer high potential to achieve more efficient and ecologic tunnelling with regards to a significant decrease of resource consumption. This holds for the high amount of time the challenging tunnelling projects still need, but also the corresponding requirements of financial and material resources.
The technology Swissloop Tunneling has been conceptualising, developing and testing, for almost four years, while continuously has made progress also needs to be analysed on possibilities for scaling up.
The project is investigating the use case in micro tunnelling with its current MTBM ‘Groundhog Beta’, which currently remains a prototype machine with a diameter of 0.606m. This opens an R&D opportunity for the team of students to assess to what extent the machine could be scaled up to construct a larger tunnel diameter.
This is only one of various open questions the team wants to answer during the upcoming seasons of the ongoing student-led R&D project. The process of conducting solution-oriented R&D to contribute to innovative tunnelling solutions is what drives the team members. It also gives the engineering students valuable insights and practical experiences with regard to what it means to implement challenging approaches to innovation.
FUTURE AND INDUSTRY CONTACT
Swissloop Tunneling is looking forward to the future of the project and staying in touch with the international tunneling industry.
Innovation in complex areas, such as tunneling, asks for a continuous exchange between the industry representatives. All are facing technological as well as economic challenges of tunnelling construction. But one thing is for sure – they all together are contributing to delivering the important infrastructural requirements of society in future. This is where Swissloop Tunneling strives to take part by continuously testing profoundly new approaches for tunneling innovation.
SWISSLOOP TUNNELING: PARTNERS
The following is a list of partners supporting the R&D work of the student-led team in Swissloop Tunneling:
Founding Partners: ETH Zurich; Empa Partners in 2023/24, by level:
Exclusive: Hagenbuch
Diamond: Sika
Platinum: Glencore; rollstar; Implenia
Gold: Hansa-Flex; Klüber; Endress+hauser
Silver: K&V; Kohler; Campus Sursee; Jorimann; SKF
Bronze: Orell; SVS; Kaeser; Schneider Electric; Sieber; Krohne; Swiss Tunnelling Society (STS); Vulkan; Indel; Frutiger; Kindlimann; Lastech; Nagra.
Patron: Spanset; Doka; Alfred Müller; Petrig; Weiss Transporte; Isey Skyr; Blickle; Q_perior