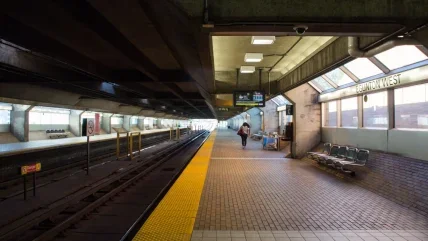
Introduction
Cedarvale station was built as part of the new
Eglinton Crosstown LRT in Toronto, at the intersection with the Yonge-University (Spadina) line under the existing Toronto Transit Commission (TTC) boxed tunnel of the Eglinton West Station. The new station, an open-cut excavation, required an underpinning of the operational TTC box to ensure an unhindered service.
A novel solution was implemented to provide access to install a series of ‘needle beams’, utilising six small, mined galleries. The galleries were supported by a temporary shotcrete lining on their sides and a concrete slab at their invert. Rebar dowels were placed at the connection of the shotcrete lining to the overlying TTC box base slab. Additionally, temporary support was provided during the excavation of the galleries by a series of steel props, supported on precast concrete pads, mechanically connected to the invert slabs.
All the excavations extended below the groundwater level. Dewatering was undertaken prior to the excavation of the galleries to lower the groundwater level to below their invert level and to control groundwater ingress and surface water flow during excavation.
The TTC box and the new Cedarvale station as well as the main underpinning elements are shown in Figure 1.
The multidisciplinary design team on the works consisted of Dr. G. Sauer & Partners (mined elements), Entuitive (structural), and Isherwood (support of excavation). The prime contractor of Cedarvale station was Crosslinx Transit Solutions Constructors (CTSC), a construction consortium of SNC Lavalin Inc., ACSDragados, Aecon Infrastructure, and EllisDon Civil. Sub-contractor for the mining works was HC Matcon Inc. (HCM).
Existing Station
The existing TTC box is formed of reinforced concrete units, 12.2m-long, 10m-wide and 5.7m-high. The top and bottom slabs and the external walls are approximately 600mm-thick and the inner wall is approximately 460mm-thick.
Existing Units (from South to North) 1604, 1608 and 1612 (see Figure 1) were expected to be impacted by the mined gallery excavations.
Connection plates (patches) were installed at the external faces of the TTC box following the removal of the soil cover, to minimise the differential movements of these units during the ongoing excavation works (see Figure 2).
The station had to remain operational during the construction works. To ensure the smooth operation of the railway, real-time monitoring of the unit joint movements was utilised with the stringent alert level of 3mm differential displacement between the joints of adjacent units.
Ground Conditions
The soil deposits in the project area are a result of glacial depositional systems resulting in a complex distribution of heavily overconsolidated hard plastic glacial till layers, separated by interstadial stratified deposits of very stiff to hard clays and very dense, non-plastic, silt, and sand.
The upper groundwater is about 3m to 6m below ground surface, meaning that the excavation of the galleries extended below the groundwater level. Groundwater ingress could occur from perched groundwater, surface water flow, and from more permeable sand/silt layers within the plastic clayey deposits.
Dewatering of the permeable soil layers was implemented using deep wells prior to underground excavation in order to lower the groundwater level and to control groundwater inflow, mainly as part of the subsequent, main station excavation works. The geotechnical properties used in the design are summarised in Table 1.
Underpinning System
The underpinning system consisted of a series of needle beams transverse to the alignment, installed through the six mined galleries. The two ends of the needle beams were supported during construction on temporary steel girders founded on caissons, and in the permanent configuration were connected to reinforced concrete wall-beams integral to the station structure. A jacking system provided the means to adjust the elevation of the needle beams and compensate for potential excessive movements, based on the real-time monitoring of the TTC box.
Six mined galleries were constructed in total, as shown in Figure 3, supported by a continuous lining of fibre reinforced shotcrete (FRS) at the sides, structurally connected to the invert slab. Each of the six galleries was divided longitudinally into eleven advances, typically 1.1m-long, excavated simultaneously from both sides.
Galleries 1A, 1B, and 2 which were excavated first, were 4m-wide by 2.75m-high, U-shaped with a cross section as shown in Figure 4. The walls were supported by a 100m-thick shotcrete lining, following a concave shape, increasing to 300mm at the top connections to the TTC box. A first, 100mm-thick shotcrete layer was applied immediately against the sides of the exposed ground concurrently with the full thickness of the invert, whereas the completed profile of the sides was applied in a subsequent step. The invert slab was FRS, 350mmthick, cast-in-place.
Gallery ‘1A Extended’ was essentially an enlargement of Gallery 1A with a concurrent removal of its left-side wall and shares the same geometrical characteristics. Only its left side was supported by the full shotcrete lining whereas the invert slab is similar to the other galleries.
Galleries 3 and 4 were excavated between the completed Galleries 1A, 1B and 2, and they did not require side support.
A 50mm-thick shotcrete layer (flashcrete) was sprayed against the exposed excavation faces in all galleries.
The support system was supplemented by a series of temporary, vertical steel props, installed sequentially at every excavation step next to both sidewalls of each gallery, except for Galleries 3 and 4. The props were supported on precast concrete pads, 500mm x 500mm x 250mm, mechanically connected to the 350mm-thick concrete slab. Every set of props was connected (in the transverse direction) with a set of connecting beams.
Design Considerations
The gallery excavation and support was simulated using 2D Finite Element analyses assuming plane strain conditions. These analyses were used to model the excavation sequence and calculate the lining stresses.
The existing reinforced concrete TTC box was simulated as shown in Figure 5. The four joints between the segments were introduced as physical discontinuities.
An interface was additionally introduced between the TTC box base slab and the underlying soil to capture the soil/structure interaction as realistically as possible.
The joint was a frictionless interface with stiffness parameters corresponding to those of the soil and a Mohr Coulomb slip criterion. This interface allowed the normal separation between the structure and the underlying soil.
The analysis also accounted for moving train loads and seismic loads. The calculated displacements of the most conservative analysis are shown in Figure 6.
Construction
Construction Sequence of Galleries
Prior to the start of the construction works of the mined galleries, the installation of the structural steel waler beams in front of the existing TTC box had to be completed. The horizontal beams rest on top of deep foundation piles and are structurally bolted against them, providing end support for the needle beams. The excavation of the first two galleries, 1A and 1B, commenced on 30 September 2019. To reach the actual ground level below TTC box, access cuts within the beams had to be excavated and supported by 200mm-thick FRS shotcrete. Each gallery was then advanced from both sides to accelerate the overall construction schedule and to allow symmetrical supporting of the TTC box. The excavation works of the Galleries 1A and 1B were finalised by the end of October (see Figure 7).
Once all vertical steel props had been jacked in Galleries 1A and 1B, the structural needle beams were installed, and excavation works of Gallery 2 commenced on 4 November. Gallery 2A was fully excavated and supported on 11 November. Subsequently, the needle beams in Gallery 2A were installed and, on 16 November, works of the extended Gallery 1A commenced. The removal of the south sidewall of Gallery 1A occurred concurrently with the relocation of the inner, vertical props for access purposes, as shown in Figure 8 (left). Extended Gallery 1A excavation and support works were completed on 22 November, as shown in Figure 8 (right).
Construction works continued with the installation of the needle beams in extended Gallery 1A. On 2 December, excavation and support works of Galleries 3 and 4 commenced. The typical advance length was increased from 1.1m to 2.5m since only the excavation of the remaining soil and spraying the invert slab had to be executed. No installation of vertical steel props was necessary for Galleries 3 and 4, as shown in Figure 3 and Figure 6.
Galleries 4 and 5 were completed on 6 December 2019. The total construction time of all mined galleries was just over two months. Figure 9 shows the final configuration of the underpinned TTC Spadina subway box.
Challenges during Construction
Several challenges encountered during the execution of the works are described in the following sections.
Confined Working Space
The biggest challenge in this project was working in confined space under the existing TTC subway box. The contractor faced a very tight environment caused by existing support elements, the steel waler beam, and the subway box itself. This became more challenging once the first needle beams within the galleries had been installed. The prompt and uneventful execution of the works required a skilled construction team equipped with the smallest available plant.
Grout Bags
Grout bags were placed between the vertical props and the TTC box to ensure a full connection (see Figure 10). The grout bags were installed with vertical props and precast concrete pad footings with their connecting beams before applying the first shotcrete layer. With changing weather conditions and colder ambient air temperature setting in, the grout curing time increased significantly.
TTC Box Slab / Mud Slab
During the excavation of Gallery 1B an unexpected amount of previously poured concrete underneath the TTC box base slab was encountered, which was not documented in the as-built drawings. This additional concrete appeared also in other galleries and resulted in a significant amount of extra time and work effort.
Chipping of the concrete was only permitted by hand (jackhammer) as directed by TTC. No excavator or similar heavy equipment was allowed due to working beneath the live operating subway.
Rebar Dowels
As per design, 15M rebar dowels at a spacing of 275mm had to be drilled into the TTC box before applying the second layer of shotcrete to provide a structural connection between the shotcrete lining and the TTC subway box. Prior to dowel drilling, the contractor had to scan the box base slab for embedded conduits or reinforcement, which proved to be difficult due to the uneven surface of the exposed concrete base slab.
Existing Drainage Pipe / Manhole
According to as-built information of the TTC box, an abandoned drainage manhole and a drainage pipe were located underneath the Eastbound box. The exact location was not known and was identified during the excavation works. The manhole was encountered between Gallery 1B and Gallery 4 and the drainage pipe itself was running in the north-south direction. Special attention was paid when removing the drainage pipe, since the pipe’s material contained asbestos. The asbestos was tested ahead of the construction start and identified as Type 1 (low risk). Nevertheless, once the drainage pipe was exposed, a separate firm specialised in handling and removing construction material containing asbestos carried out the removal in a safe manner.
Monitoring
The entire live operating TTC Spadina subway tunnel and the mined galleries were continuously monitored during all tunnel construction activities.
Optical monitoring targets were installed in the gallery sidewalls, six in total within each gallery. The red trigger level was 8mm inward displacement. The readings in all the targets indicated a stable condition during the entire gallery construction period with maximum recorded displacements in the range of 2mm.
Additional to the in-tunnel monitoring, the entire TTC tunnel, including the rail tracks, were monitored in real-time. Inside the tunnel, electric level beams and tiltmeters were installed. Additionally, the contractor installed Building Monitoring Points (BMPs) outside the TTC tunnel box to monitor the exterior walls/roof of the TTC box.
The differential settlement readings of the rail tracks within the relevant monitoring tunnel box units (underpinning zone) ranged between 0mm and 2mm throughout the construction of the galleries. The alert level of 3mm was breached twice on one single instrument inside the TTC subway tunnel but the reading was discarded as a false reading due to temperature fluctuation. No action response by TTC and the contractor was required.
Conclusions
A novel underpinning solution of the operational TTC Eglinton West station for the construction of ECLRT Cedarvale station was undertaken utilising a series of small, mined galleries. These galleries provided access to install a supporting system of steel (needle) beams. The main challenges were the confined space and the tight differential displacement criteria of the TTC box. The construction of the mined galleries was completed in just over two months. The impact of the works on the operational subway was negligible.