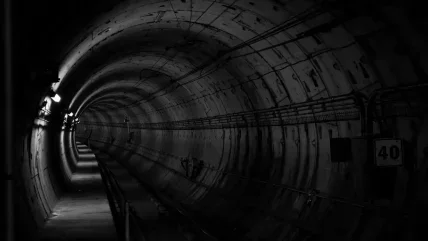
For decades, the tradition for new bored tunnel projects has been to cast segments and erect master rings of the lining, although this is done horizontally and rests on a flat surface. The objective is to demonstrate compliance with the required dimensional tolerances of the cast segments and so provide the necessary assurance for the tunnel lining being erected behind a tunnel boring machine (TBM).
The requirements for master ring builds vary by project. On some, the tenders may require that on top of the master ring level there is to be erected a further concrete ring, occasionally yet another, in the horizontal assembly. The stacked additional ring is a trial ring. A project may also seek that the master ring assembly is repeated at intervals throughout the duration of precast segment production during the bored tunnel project.
Constructing master rings, and trial rings, are both challenging and risky tasks for the workforce in the casting factory, especially for large diameter segmental concrete tunnels. Unlike in a tunnel where vertical rings are constructed, at the factory the horizontal assembly of a master ring often required a truck-mounted crane. In some cases, it can take up to a week to complete a master ring.
Then, there are the different tolerances to consider that combined to produce the measured geometric result. First, there is the manufacturing dimensional tolerance from the casting of the segments and their potential fit; second, there is the spatial tolerance that arises from the workers’ efforts to assemble the rings, and horizontally, under lifting but also ring loading conditions that are not what happen in the tunnel – including the presence of gaskets.
To focus more on the casting quality in its dimensional tolerance, a tool is needed to give that focus alone: this can come from the concept of virtual rings.
Virtual master rings have the potential to replace this tradition of building segments horizontally, outside the factory, by instead using digital systems to ‘assemble’ master rings. It would be a shift from physical to digital.
The data to enable the ‘assembly’ comes from the map of 3D coordinates produced by laser tracker measurements of cast segments or the segment moulds themselves. With the data map of the dimensional tolerance the fit of the virtual segments into a virtual ring is rapidly possible.
Construction assembly tolerances are to be considered separately, by the contractor. The virtual approach enables a sharper focus on the core purpose of master rings – the casting quality, prior to the segments reaching the tunnel.
In building a virtual ring, therefore, a submillimetre accuracy can be achieved, the alignment of neighbouring circumferential and ring joints observed, and the fit of bolt holes checked. The traditional method, on the other hand, is discussed controversially despite the significant amount of work and risks – particularly as the horizontal position of the ring and absence of gaskets do not simulate the reality in the excavated tunnel.
VMT has helped develop the potential for virtual master rings by working on 20 projects where the digital approach has been undertaken, in different degrees, alongside the traditional method of assembling the physical rings. This has been, very much, a verification phase of the concept and working technology, proving the validity and demonstrating how time and cost could be saved in future, especially should a project move toward a mostly or wholly virtual master ring approach.
Among the key projects so far using both physical and virtual master rings is a section of London Thames Tideway project, but an adjustment was made on that project to reduce the need for so many built master rings. The new Gotthard road tunnel 2nd tube project, in Switzerland, is using virtual master rings for part of its pilot tunnel.
SPECIFYING REQUIREMENTS
A number of reasons exist for specifying extremely tight dimensional, and so geometrical tolerances, for cast concrete segments and these are listed in standard specifications issued by associations like the International Tunnelling Association (ITA) or the British Tunnelling Society (BTS). They are a variety of reasons for master rings to be built and they are:
- A full ring is geometrically sensitive to inaccuracies and distortions in segments
- High load effects coming onto the lining from earth, water, and grouting pressure
- Jacking forces applied to the rings by an advancing TBM during boring
- Load transfer might take place only in limited areas (partial surface load)
- Damage is not always visible or detectable (e.g., on the outer side of a ring)
- Repairing damaged segments is both costly and time-consuming
Tapered rings enable the tunnel lining to accommodate alignments that contain curves or to compensate for misalignment of the tunnel due to site-specific problems. The use of reinforced segments necessitate precise segments, and great care in their installation is needed.
BUILDING MASTER/TRIAL RINGS
Geometrical tolerances of a ring are defined in a project’s specification and erection of the master ring first, and possibly a trial ring placed on top, is a basic requirement, even though the process is complex and time consuming while not being in the proper environment.
It takes anywhere from several days up to a full week to build a master ring and then perhaps add an additional trial ring on top, if that is necessitated in the requirements. These efforts require huge man-power and logistical resources. A difficult, heavy-weight challenge in itself, while helped by use of cranes the uncommon task can be a health and safety challenge.
But this work not only must happen at the beginning of segment casting and before tunnel boring commences but also through the production period, all of which multiples the efforts and costs.
Yet, for all the time and cost, and challenges, the master ring assembly on the flat ground surface does not fully represent the arrangements experienced for a ring build behind a TBM due to, for example, the different orientation, absence of installed gaskets, there being no pressure from jacking forces, etc.
MEASURING THE RINGS
Metrology companies perform mould and segment 3-D measurements as well as master and trial ring 3-D measurements using a laser tracker system. Portable laser trackers are used to measure large parts, jigs, moulds, assemblies, and machines on-site, quickly and easily. They measure 3-D coordinates by tracking a reflector moved across an object being measured and the data collected can be compared against nominal CAD data, allowing the team to move forward with confidence or make appropriate adjustments.
These measurements are performed using a premier portable metrology software for large-scale applications, which has been adapted for this specific task. Specified measurement profiles are used for collecting the data and specified measurement plans (programmed scripts) are used for an immediate and fast semi-automated calculation and reporting procedure.
For example, on one master/trial ring for a rail project in Germany the results showed a horizontally assembled concrete segmental ring, as arranged on the ground horizontally, to be a significantly deformed ellipsoid rather than a circle, in that it had unacceptable deviations ranging from -9.4mm to +7.8mm. The workers that assembled the rings confirmed there were difficulties erecting the heavy concrete segments to form the ring when using cranes, chain blocks and belts.
Furthermore, only the master ring’s intrados and extrados cylinders could be measured. The adjacent and hidden joints could not be measured and therefore controlled.
Looking at these unsatisfying measurement results, the virtual ring build concept was introduced as an alternative to full physical assembly, aiming to get more focus on the quality of segment manufacture independent of complications of challenges with ring assemblies.
TAKING AN ALTERNATIVE APPROACH
Instead of building a physical ring, the alternative concept proposes to measure individual segments or moulds followed by an assembly of these results in the virtual world.
Advantages of taking the virtual assembly approach for the master/trial rings are seen to include:
- Quality control for a complete ring
- Avoiding the master/trial ring construction and its inaccuracies due to physical limitations
- Realising and eliminating possible physical ring build problems caused by geometrical effects prior to the segment transportation into the TBM
- Prove that segments from different mould sets can be combined within one ring, if this is not allowed in the project’s specification
- Prove that segments exceeding the minor submillimetre tolerance can be combined within one ring and still meet the ring build tolerances; ultimately decreasing the production’s reject rate
- Saving time and costs
- Avoiding health and safety risks to onsite personnel
In taking this approach, when the actual individual segment measurements from the trial ring described above were taken alone then their assembly, virtually, was shown to be more accurate compared to the trial ring that was physically assembled with them, due to the construction challenges. The measured deviations of the virtual assembly ranged from only -1.9mm to +1.5mm.
The virtual assembly approach, therefore, is a practical solution to prove the ring build quality for segments in mechanised tunnelling.
TECHNICAL PROCEDURE
The 3-D measurement scan data of each mould or cast concrete segment are combined mathematically such that adjacent moulds or segments are gathered into an assembly of the bored tunnel lining ring.
This Virtual Ring Build is realised through so-called mathematical relationships, which is a powerful method with a number of uses: dynamic inspection, alignment, virtual fit-up, real-time assembly and optimisation.
Relationships, though, are not physical objects by themselves but rather they provide a defined link between objects.
In the simplest case, a relationship calculates the distance between two related entities and recalculates this distance whenever either of the related items are moved. This linking process is quite efficient and can be expanded to include many points and many objects simultaneously – in this case, many point groups from the individual measurements and many objects from all the segments nominal CAD.
MATHEMATICAL CALCULATIONS
The following calculations are performed for a virtual ring: – Relationship fitting of the measured intrados points to the nominal intrados cylinder
- Relationship fitting of the measured front and back points to the nominal circumferential joint
- Relationship fitting of the measured left and right points to the corresponding adjacent actual longitudinal joint
- Using constraints of only positive residuals in the adjacent longitudinal joints, as neighbouring concrete joints physically cannot overlap
The resulting 3-D deviations to the nominal ring as well as the resulting gaps and laps at the adjacent joints are presented as a graphical output, showing variations from theoretical measurement.
CONSIDERATION IN TUNNELLING TENDERS
To date, 3D mould and segment measurements are a common best practice for physical master ring builds, but the possibility of building virtual rings is not yet published by the industry nor specified in a remarkable portion of segmental lining tenders.
The format and contents of a Virtual Ring Build report are not defined and standardised. However, the graphical and numerical layout described here have been accepted by a dozen VMT clients on major tunnel projects across the globe. In those cases, the Virtual Ring Build is only supplementary to, and complementary to, the required 3D physical master ring builds that have taken place.
To allow contractors to move to adopting and utilising the Virtual Ring Build approach alone the industry would need to reflect this possibility in tenders with changes to the corresponding sections as part of the segmental lining specification.
SPOTLIGHT: THAMES TIDEWAY TUNNEL
London relies on a 150-year-old sewer system built for a population less than half its current size. The Thames Tideway Tunnel project is a large-scale upgrade to the capital’s sewerage system to cope with its increased and growing population. The project is based around a 25km-long tunnel that will intercept, store, and ultimately transfer sewage and stormwater waste away from discharges into the River Thames.
Starting in Acton, west London, the sewer tunnel passes through the heart of London at descending depths of between 30m and 60m, using gravity to convey the flows of waste eastwards. The construction works on the large project are divided into three sections, each of them under construction by a different contractor.
One section of the specification for the precast segment requirements of this large infrastructure project contained a mandatory clause to erect physical trial rings at intervals not exceeding 0.5% of the segment production and compare these against the master ring. Applying this clause on the C415 East Section (Greenwich and Main Tunnel Works) with a total production of around 39, 000 individual elements, the contractor was asked to build and erect 30 trial rings during the precast production.
This procedure had a large negative impact on the contractor’s project budget and limited benefit for the client, which created the willingness to investigate alternative solutions. After a technical seminar, both parties explored the possibility of replacing all physical by virtual rings with the exemption of the first master ring on each tunnel, which would change a plan for 30 physical master rings to only two plus 28 virtual build rings.
Furthermore, results from dozens of segment measurements were already available due to regular quality checks in the factory. Therefore, the decision to submit a change request was taken by the contractor and unanimously approved by a project manager’s instruction.
All images courtesy of VMT.